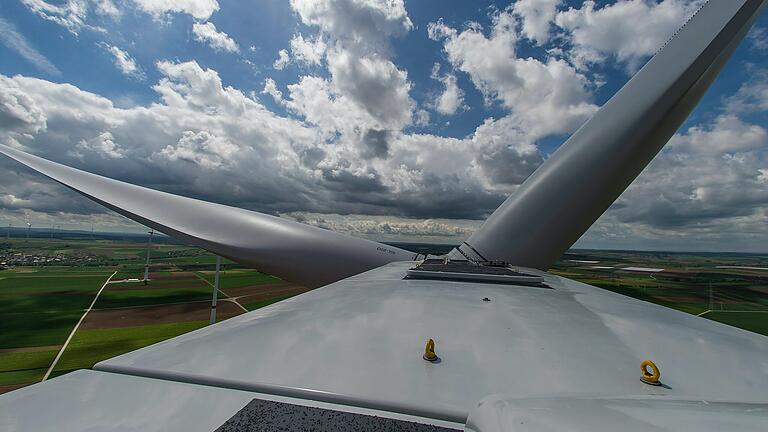
Ein Stück Industriegeschichte steht hier, ein Stück Schweinfurt, ein Stück Zukunft. Die Rede ist von Werk 3 von SKF, am 6. Mai 1971 als Fabrik auf der "grünen Wiese" eröffnet. "Der Blick ist freier. Die Luft ist sauberer", hieß es damals vor 50 Jahren bei der Eröffnung. Der Sprung über den Main, in das unter Oberbürgermeister Georg Wichtermann erschlossene Gewerbegebiet Hafen, wurde Mitarbeitern und Stadtgesellschaft in den allerschönsten Worten ausgemalt: "Und vom nahen Wald ein Hauch Frische", schrieb SKF in einer Mitteilung zum Jubiläum.
Von der Autofabrik zur Windkraft
Werk 3 war anfangs eine "Autofabrik". Gefertigt wurden Rad- und Getriebelager. Heute geht es um Windkraft. Gigantische Rotorlager wie das SKF Nautilus mit einem Durchmesser von vier Metern, am Standort Schweinfurt gefertigt, sichern hunderte Arbeitsplätze. Knapp 900 Beschäftigte arbeiten hier. Etwa genauso viele wie vor 50 Jahren. Seit 2017 hat das Werk einen futuristischen Nachbarn: Das SKF Sven Wingquist Test Center. Was von außen aussieht wie eine Raumstation ist das leistungsfähigste Großlager-Prüfzentrum der Welt: ein 40-Millionen-Projekt.
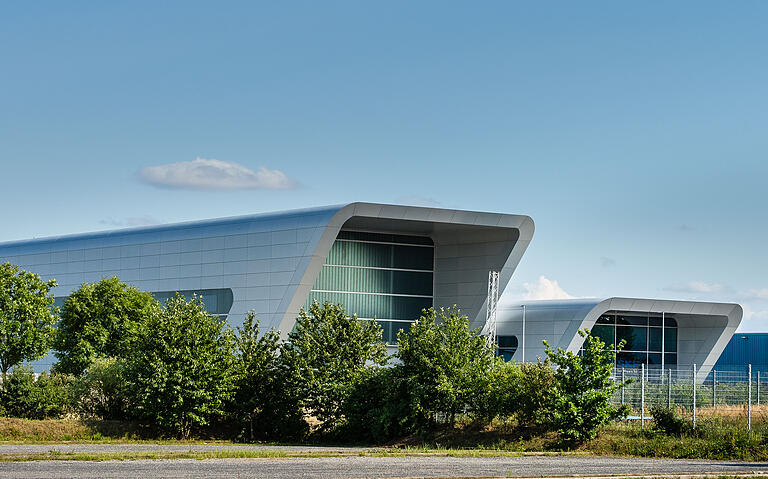
Windkraft Kerngeschäft bei SKF
Windkraft hat sich zu einem wichtigen Bestandteil von SKF entwickelt, erzählen Martin Johannsmann, SKF-Deutschlandchef, und Martin Göbel, der Leiter des Testzentrums. "Wind ist ein Kerngeschäft bei SKF", betont Martin Johannsmann. "Wir gehen davon aus, dass es sich weiterentwickelt." Generell spiele das Thema erneuerbare Energien eine große Rolle bei SKF. Unter anderem baut SKF die Turbine für ein schottisches Gezeitenkraftwerk.
Die Nachfrage nach den Lagern, die für Windkraft produziert werden, war so groß, dass das Werk teilweise an der Kapazitätsgrenze war, sagt Johannsmann. Schweinfurt ist übrigens eines der drei Werke weltweit, in denen Großlager für Windkraft gebaut werden. Die anderen beiden SKF-Standorte sind in Göteborg in Schweden und in Dalian in China. In China verzeichne man den größten Zuwachs an Windenergie, auch Indien sei ein wichtiger Markt.
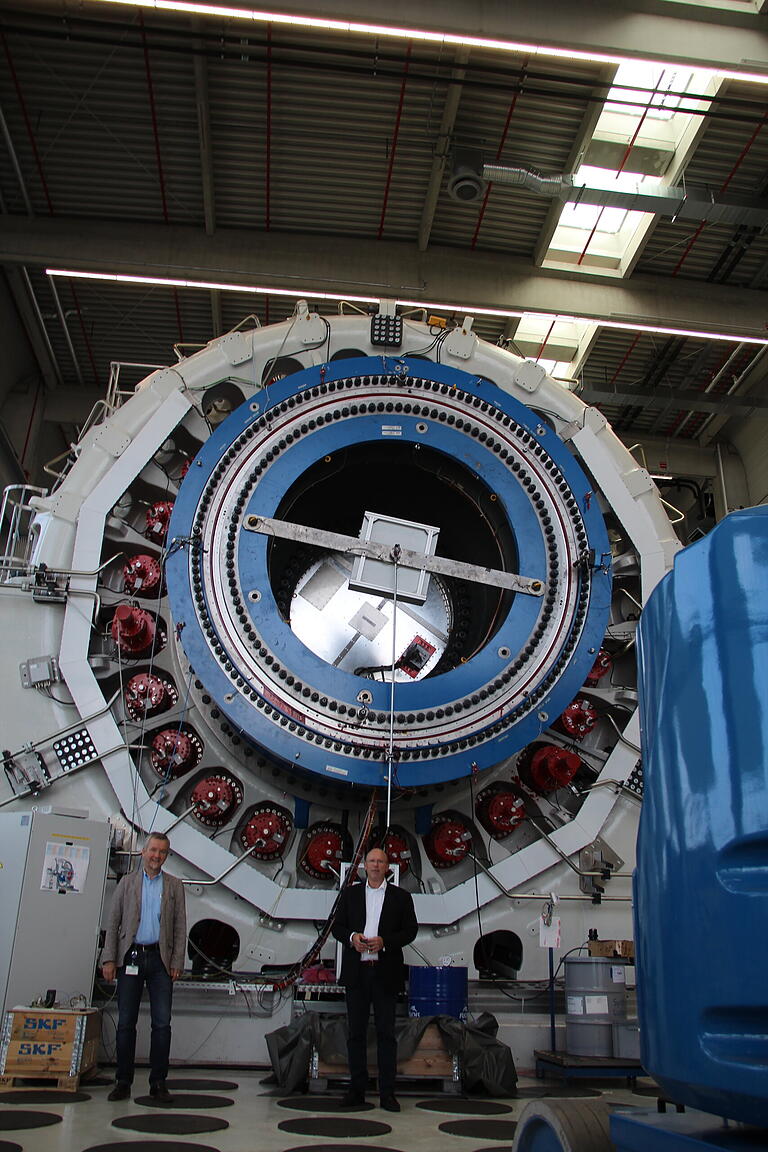
Was wird genau im Test Center gemacht?
"Wir haben einen Teststand gebraucht, um die Grenzen der Großlager zu sehen", sagt Martin Göbel. In der Halle lässt sich ein Jahrhundertsturm simulieren. Auf den beiden Prüfständen des "Sven Wingquist Test Centers" werden die Lager extremsten Belastungen ausgesetzt. "Der größere Prüfstand kann Lager mit einem Außendurchmesser von bis zu sechs Metern aufnehmen. Der etwas kleinere Prüfstand treibt Großlager für den Schiffbau, den Bergbau, die Papierindustrie oder auch den Zement- oder Stahlbereich an ihre Belastungsgrenze", hieß es 2017 in unserem Wirtschafts-Jahresrückblick. Laut Martin Göbel sei das Test Center das einzige weltweit, das nicht nur ein einzelnes Hauptlager für Windturbinen testen kann, sondern eine komplette Lagerungseinheit. Johannsmann formuliert das so: "SKF investiert in technische Marktführerschaft."
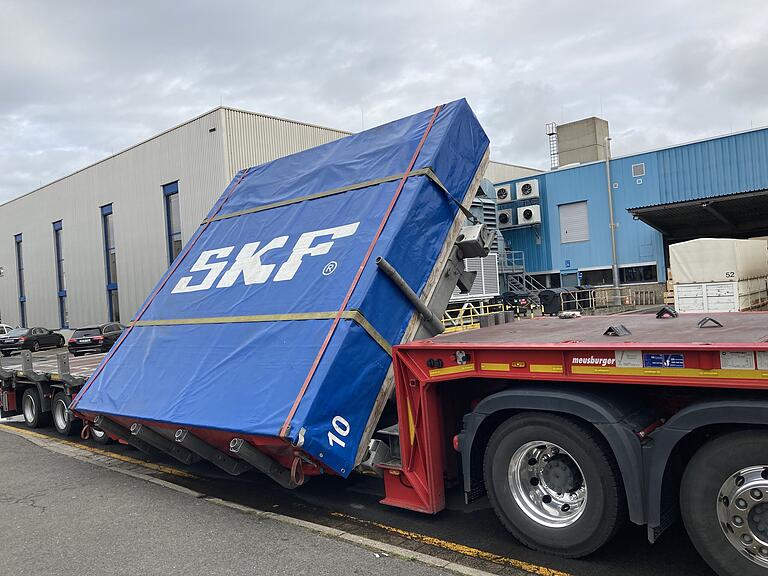
Das Test Center hilft aber auch bei der Grundlagenforschung, so Martin Göbel. Es gehe nicht um Qualitätstests. "Qualität wird produziert", sagt er. Zum Beispiel im Werk 3, ein paar Schritte entfernt. Bei den Tests gehe es um die Festlegung und Entwicklung der Konstruktionsregeln. Realitätsnah werden kritische Betriebssituationen hervorgerufen. Auch um das Thema Zustandsüberwachung geht es. Alles, was man von extern kontrollieren und steuern kann, macht den Windradbetreibern das Leben leichter und effizienter. Die Tests sind auch ein Teil des Risikomanagements der Betreiber. Ein dreimonatiger Test zu Beispiel kann die Weichen dafür stellen, dass eine Anlage 20 bis 25 Jahre hält. "Lagerwechsel ist teuer, speziell bei off-shore-Anlagen", sagt Johannsmann.
Warum Gewicht ein Faktor bei Windrädern ist
Ein Riesenthema laut Göbel bei Windrädern: Gewicht sparen. Weniger Gewicht heißt logischerweise weniger Materialkosten. Weniger Gewicht heißt aber auch, kleinerer CO2 -Fußabdruck. "Je leichter, desto besser." Im Vergleich zu den ersten Windrädern sei die heutige Generation um gut 30 Prozent leichter. "Mit dem gleichen Gewicht erzielen wir heute drei bis vier Megawatt, wo früher zwei Megawatt möglich waren", betont Martin Göbel. Eine weitere Messlatte gibt es noch: "Was kostet die Herstellung einer Kilowattstunde Strom?"
Apropos Messlatte: Die Lager, die in der Halle getestet werden, sind riesig. Martin Göbel und Martin Johannsmann wirken winzig, als sie sich dem Prüfstand nähern. Damit die Halle nicht zu eng wird, haben sich die Konstrukteure und Architekten etwas ausgedacht. Durch das Portal passt alles, das unter einer deutschen Autobahnbrücke durchpasst. Auch was futuristisch aussieht und einen Architekturpreis bekommen hat, muss funktionieren können.
Und manchmal muss man eben praktisch denken, auch bei den ganz großen Dingen. Zwölf Tonnen wiegen die Großlager, die im Schweinfurter Werk 3 entstehen. "Diese Hauptlager halten den Rotor", erklären Johannsmann und Göbel. Gut 150 im Jahr verlassen das Werk. Sie stehen schräg auf den Transportern. Das sorgt dafür, dass das keine Sondertransporte sind. Und dafür, dass man die Lager made in Schweinfurt sofort erkennt, wenn man an einem Schwertransporter auf der Autobahn vorbeifährt.