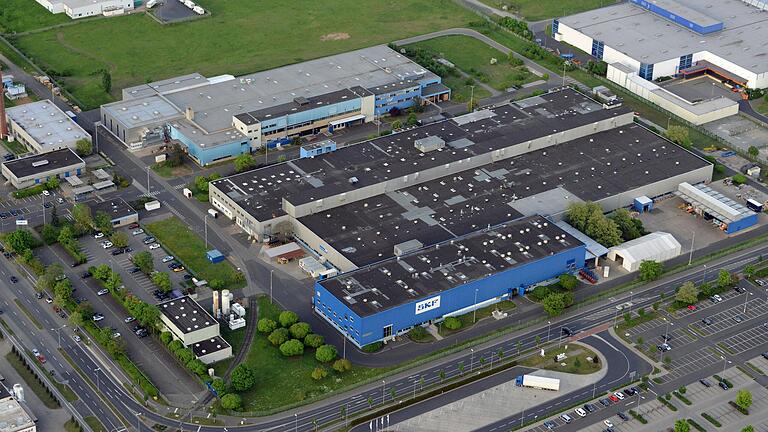
In der einstigen "Fabrik auf der grünen Wiese" fertigt SKF heute auch Windkraft-Großlager und arbeitet an einer nachhaltigen Zukunft. Vor 50 Jahren hat SKF sein Werk 3 im Schweinfurter Gewerbegebiet Hafen eröffnet.
Eine "Fabrik auf der grünen Wiese", so erfuhren die Gäste bei der Einweihung des Schweinfurter SKF Werk 3 am 6. Mai 1971, hat so manche Vorteile. "Der Blick ist freier. Die Luft ist sauberer." Der Sprung über den Main, in das unter Oberbürgermeister Georg Wichtermann erschlossene Gewerbegebiet Hafen, wurde Mitarbeitern und Stadtgesellschaft in den allerschönsten Worten ausgemalt: "Und vom nahen Wald ein Hauch Frische."
In einer Pressemitteilung erinnert SKF an das Jubiläum. Werk 3, das war damals eine modern konzipierte Hochleistungsfabrik des auch noch in Backsteinhallen an der Schrammstraße nahe der Schweinfurter City produzierenden Wälzlagerherstellers SKF. Herzstück war das mächtige Fabrikationsgebäude Bau 310 mit knapp 30 000 Quadratmeter Nutzfläche für Produktion, Büros und Sozialeinrichtungen wie einer Kantine mit 432 Sitzplätzen, durch deren lichtdurchflutete Fenster man freien Blick auf das SKF Verwaltungshochhaus auf der anderen Mainseite genoss.
Die „Fabrik im Grünen“ verfolgte ein damals wegweisendes Umweltschutzkonzept. „Alle Maschinen, an denen Öldämpfe und auf andere Weise Luftverschmutzung auftreten kann, sind mit Abzugshauben versehen und an zentrale Absauganlagen abgeschlossen. Über Elektrofilter wird alles ausgeschieden, was zu einer Verunreinigung der Umgebung und des Luftraums über unserer Fabrik führen kann“, verlautbarte SKF bei der Einweihung vor einem halben Jahrhundert. Machtlos waren diese Filter allerdings 1988 bei einem Großbrand im Werk 3, der ohne größere Personenschäden abging, aber 100 Millionen Mark Schaden verursachte.
Massenfertigung in der „100 000-Lager-Fabrik“
Werk 3 war anfangs eine „Autofabrik“. Gefertigt wurden Rad- und Getriebelager in großer Stückzahl für alle namhaften Hersteller. Gleichzeitig hat sich gerade dieses Werk immer wieder neu erfunden und steht fast sinnbildlich für die Unternehmensentwicklung bei SKF. Beispiel Fertigungsprozesse: In den 1970er-Jahren war so genannte Batch-Fertigung noch aktuell und die Wälzlagerkomponenten – Innenringe, Außenringe, Wälzkörper, Käfige – wanderten von Maschinenpark zu Maschinenpark, wo sie teils mehrstufig bearbeitet wurden. „In der Seitendurchmesserschleiferei wurden in mehreren Durchgängen nur Seitenringe geschliffen“, erinnert sich der frühere Fertigungsleiter Klaus Fischer, „das war ein Höllenkrach und Lärm!“
Fischer war in den 1980ern beauftragt, das Werk auf moderne Linienfertigung umzustellen – so genannte "channel production". Die Bearbeitungsschritte wurden in Reihe geschaltet und über SKF Flexlink, ein modernes Transportsystem, verbunden. Von einigen tausend Lagern am Tag stieg der Ausstoß auf 20 000 Kegelrollenlager pro Fertigungsstraße und rund 100 000 Lager täglich – industrielle Massenproduktion in Reinkultur.
Umstieg auf Großlager, Einstieg in die Windkraft
Um die Jahrtausendwende erlebte Klaus Fischer dann die nächste Umwälzung im Werk mit. Trotz Automatisierung ließen sich Massenprodukte wie Automobil-Radlager in Deutschland nur noch schwer zu konkurrenzfähigen Preisen fertigen. Der SKF Konzern verlagerte solche Linien damals aus den europäischen Werken nach Indien und Brasilien und sorgte gleichzeitig für neue Auslastung. Werk 3 wurde zum Kompetenzzentrum für mittelgroße und große Kegelrollenlager, wie sie im Maschinenbau und in Getrieben und Motoren des Schwerlastverkehrs benötigt werden.
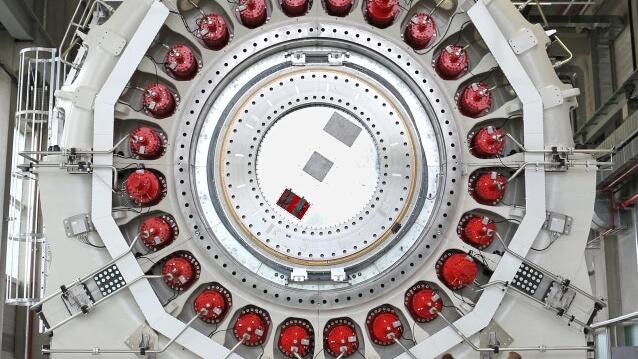
Dieser Schritt war die Basis für den Einstieg in ein lukratives Geschäft, das zehn Jahre später richtig Fahrt aufnahm: die Windkraft. Heute werden gigantische Rotorlager wie das SKF Nautilus mit einem Durchmesser von vier Metern am Standort Schweinfurt gefertigt und sichern hunderte Arbeitsplätze. Knapp 900 Beschäftigte verdienen im Jubiläumsjahr 2021 ihr Geld im SKF Werk 3, etwa genauso viele, wie vor 50 Jahren. Klaus Fischer erklärt: „Die anfängliche Batch-Fertigung war personalintensiv. Mit dem Einstieg in die Massenfertigung konnten mit der gleichen Anzahl an Beschäftigten ungleich mehr Lager produziert werden. Für die heutige Stück- und Kleinserienfertigung großer Lager spielt der Mensch in der Fertigung wieder eine wichtigere Rolle.“
Gleichzeitig wächst die Bedeutung von Hightech und Digitalisierung. Werk 3 ist auch so etwas wie eine „future factory“ von SKF. Hier gibt es einen der so genannten „World Class Channel“, eine digitalisierte, automatisierte und vernetzte Produktionslinie für die Großlager-Hartbearbeitung. In ihr zieht einer der weltweit größten Kuka-Produktionsroboter auf einem 50-Meter-Gleis seine Bahnen und verteilt die mächtigen Lagerringe auf die Hon- und Fräsmaschinen.
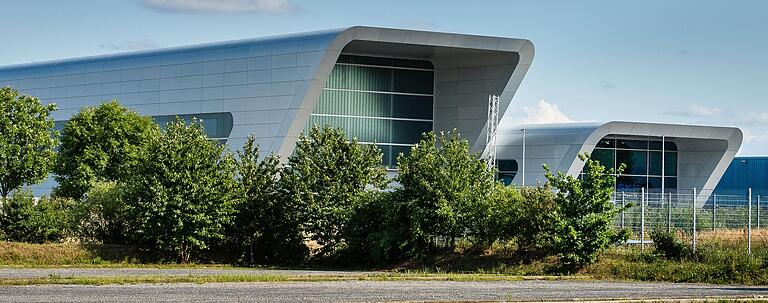
Werk 3 als Zentrum für Cleantech
Und: Hier entstand 2017 das weltweit leistungsfähigste Großlagerprüfzentrum im futuristischen „Sven Wingquist Testcenter“, wo auch radiale und axiale Einwirkkräfte auf die Rotorlager der großen Offshore-Windkraftanlagen simuliert werden können. 40 Millionen Euro hat der SKF Konzern in dieses Zukunftsprojekt am Standort Schweinfurt investiert und damit auch die grüne Agenda des Unternehmens um ein wichtiges Kapitel bereichert. Werk 3 ist heute auch Zentrum der Fertigung von Cleantech Produkten, die beispielsweise die erneuerbare Energiewende befördern.
Apropos Energiewende: Im Zuge des Neubaus einer weiteren Produktionshalle am Standort projektiert SKF derzeit auch eine Dachsolaranlage mit einer Leistung von rund 550 kW Peak. Die Anlage soll dieses Jahr noch in Betrieb gehen und spätestens im Herbst den ersten Strom liefern. Dabei erzeugt die Anlage auf ein Jahr hochgerechnet so viel Strom wie durch 150 Durchschnittshaushalte verbraucht werden. Sie ergänzt den Photovoltaikpark von SKF, der 2008 mit der Solaranlage auf dem Logistikzentrum an der Uferstraße (Werk 2) startete. SKF möchte 2030 weltweit klimaneutral produzieren. Auch in Schweinfurt werden hierfür die Grundlagen gelegt – in Werk 3, der stolzen, 50 Jahre alten Fabrik, die sich immer wieder neu erfindet.