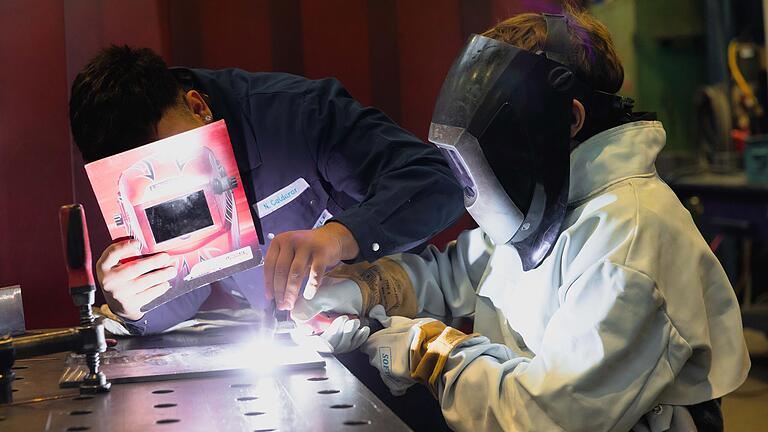
Erst heißt es, in den geeigneten Anzug schlüpfen, als Nächstes kommen die Schutzmaske sowie Handschuhe dazu – und dann kann es losgehen mit dem Schweißen. An sich nichts Besonderes beim Ochsenfurter Spezialmaschinenbauer Kinkele. Doch an diesem Tag sind es nicht die Azubis des Betriebs, die sich im hinteren Bereich einer Produktionshalle ausprobieren. Stattdessen dürfen sich Besucherinnen und Besucher unter Anleitung an die Werkbank stellen. Denn am Tag der Ausbildung öffnet das Unternehmen sein Gelände für die Öffentlichkeit – allen voran für potenzielle Auszubildende.
Fachkräftemangel trifft auch Kinkele
"Es wird immer schwieriger, junge Leute für eine Ausbildung zu generieren", sagt Matthias Groll, kaufmännischer Leiter bei Kinkele. Aktuell gebe es im Betrieb um die 30 Auszubildende. Früher waren es – verteilt auf alle Ausbildungsjahrgänge – bis zu 60 Nachwuchskräfte.
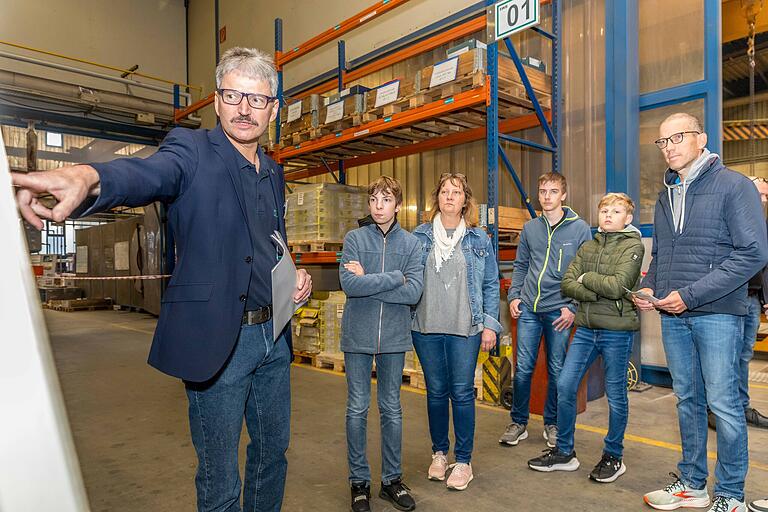
Für das Unternehmen, das derzeit etwa 280 Festangestellte beschäftigt, sei das ein massives Problem, sagt Groll. Denn auf dem Arbeitsmarkt Fachkräfte zu finden, die die nötigen Qualifikationen mitbringen, sei ebenfalls schwierig, der bundesweite Fachkräftemangel in Industrie und Handwerk auch für Kinkele deutlich zu spüren. Personal ist ihm zufolge mittlerweile zu einem limitierenden Faktor geworden. "Wir könnten mehr machen, wenn wir die Leute dafür hätten."
Deshalb lädt der Familienbetrieb mit Sitz im Ochsenfurter Gewerbegebiet Hohestadt regelmäßig Schülerinnen und Schüler zu sich ein, um ihnen die Ausbildung in einem technischen Beruf – vom Feinwerkmechaniker über den Elektroniker bis zum dualen Studium in Ingenieurswissenschaften – schmackhaft zu machen.
Rundgänge durch den Betrieb, Gespräche mit Angestellten und derzeitigen Azubis sowie Informationsstände sollen einen Einblick geben, was Auszubildende bei Kinkele erwartet. "Viele wissen nicht, was eigentlich hinter den Berufsbezeichnungen steckt und welche Möglichkeiten damit verbunden sind", sagt Ausbildungsleiter Edwin Gernert. Das könne der Tag der Ausbildung ändern.
Ochsenfurter Unternehmen ist auf komplexe Aufgaben spezialisiert
Zu sehen gibt es auf dem Gelände einiges. Im überdachten Außenbereich warten sogenannte Beschichtungsräder auf die Weiterverarbeitung. "Damit werden Kunststoffflaschen beschichtet und geblasen, zum Beispiel für Coca-Cola", erklärt Matthias Groll. Ein Stückchen weiter befindet sich eine halbfertige Vakuumkammer, in der Produktionshalle nebenan liegen Rohlinge, aus denen Castorendeckel für die Entsorgung radioaktiver Abfälle werden sollen.
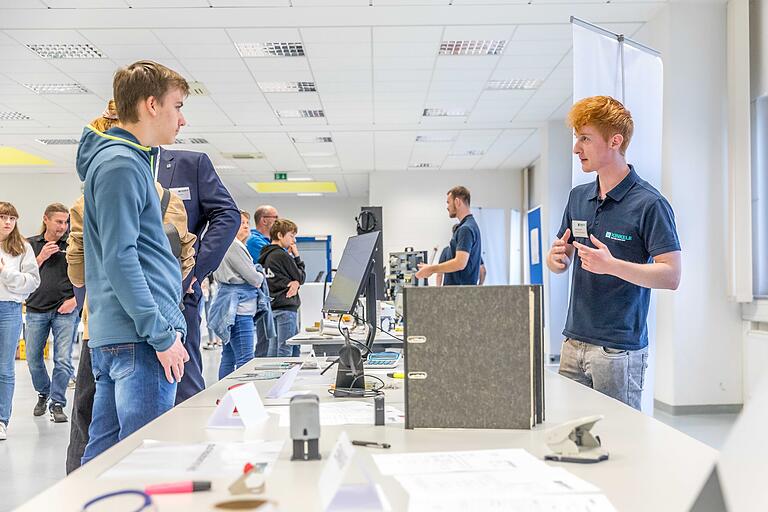
Kinkele hat sich auf besonders schwierige und komplexe Aufgaben spezialisiert. Dementsprechend ausgerüstet ist auch der Maschinenpark. "Diese Anlage kann zum Beispiel Teile bis zu 16 Meter Länge aufnehmen", sagt Groll und deutet auf eine Großzerspannungsanlage. Statt eigene Produkte zu entwickeln, übernimmt der Betrieb ausschließlich Aufträge von Kunden – darunter nicht selten außergewöhnliche. Anlagen und Teile aus dem Ochsenfurter Betrieb sind schon mit der Ariane-Rakete ins All geflogen oder treiben das größte Uhrwerk der Welt im "Royal Clock Tower" in Mekka an.
Von Auftragsflaute kann bei Kinkele nicht die Rede sein
Abseits von Nachwuchsmangel und Personalproblemen laufe es gut bei Kinkele, sagt Groll. Anders als andere Maschinenbauer könne das Unternehmen zurzeit nicht von einer Auftragsflaute sprechen, so der kaufmännische Leiter. Ganz im Gegenteil: Es fehle nicht viel zum Rekordjahr. Das liege vor allem daran, dass der Familienbetrieb für ganz verschiedene Branchen tätig ist. Fahrzeugteile, Luftfahrt, Lebensmittelindustrie, zählt Groll auf. "Läuft es in einer Branche nicht so gut, kann eine andere das wieder ausgleichen."
Aktuell seien Vakuumkammern besonders gefragt – nicht nur in Deutschland, sondern weltweit, sagt er. Ein Einsatzbereich solcher Kammern sei beispielsweise die Photovoltaik-Industrie, die sie zur Beschichtung von Glasplatten benötigt.
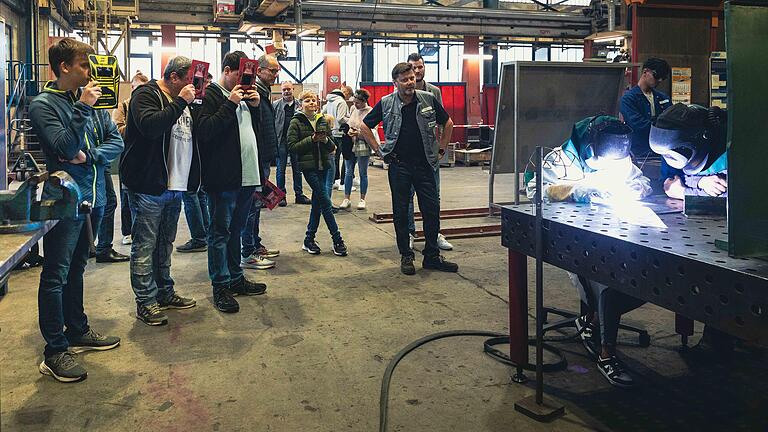
Ein Auftrag der besonderen Art ist derzeit in der Montagehalle von Kinkele zu sehen. Was für den Laien wie ein großer, gerüstartiger Arm wirkt, ist eine sogenannte Human-Zentrifuge. Am Ende des Arms soll später einmal eine Kabine befestigt werden, die dann von der Anlage mit hoher Geschwindigkeit rotiert wird. Piloten und Astronauten können sich mithilfe solcher Anlagen an im Flugbetrieb wirkende Kräfte gewöhnen.
Große Herausforderung des Projekts liege hier in der Schweißtechnik, sagt Andreas Büttner, der für die Messtechnik in der Qualitätssicherung verantwortlich ist. "Ich überprüfe mit dem Lasertracker, ob alles so ist, wie es sein soll." Sonst könnten sich ihm zufolge später unbemerkt Risse bilden. "So ein Projekt machen wir zum ersten Mal", sagt Matthias Groll. Serienfertigung gebe es bei Kinkele aber ohnehin nicht. Und genau darin sehe er auch für Azubis einen Pluspunkt: "Jeder Auftrag und jedes Bauteil ist anders. Das macht es auch für alle, die hier arbeiten, interessant."