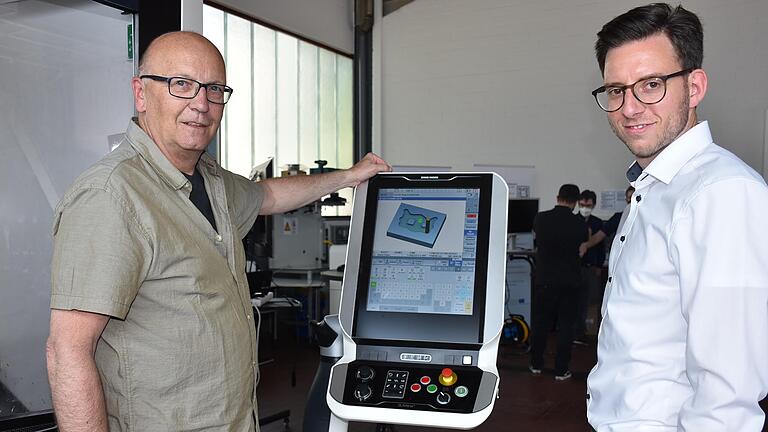
Im Rahmen der Schweinfurter "Innovation Week" hatte das Fraunhofer-Institut für Produktionstechnik und Automatisierung (IPA) zum "Open Lab Day" eingeladen. Im Oktober 2020 hatte Fraunhofer IPA seine Außenstelle in Schweinfurt in der alten Bahnhofstraße eröffnet. Hier konzentriert sich das Forschungsteam auf Künstliche Intelligenz (KI) und nachhaltig optimierte Wertschöpfung (noW), woraus sich die Zusatzbezeichnung der Außenstelle "KI-noW" ergibt.
Szenarien entwickeln, die den Unternehmen aufzeigen, welche Vorteile der Einsatz von KI in ihren Betrieben hat und wie diese in den laufenden Betrieb integriert werden können, ist der Anspruch. "Erlebbar machen, wie sich die industrielle Arbeit der Zukunft anfühlt", definierte Ingenieur Christoph Hoffmann, Projektleiter der Schweinfurter Außenstelle, das Ziel des Open Lab Days, zu dem Interessierte aus Industrie und Betrieben eingeladen waren.
Gelegenheit im direkten Austausch mit Experten und anhand von Demonstrations-Stationen mögliche Fehlerquellen im eigenen Betrieb zu erkennen, bot sich reichlich. Im Prinzip geht es immer darum, Anlagen, Produktionsprozesse und die dabei eingesetzten Werkzeuge so gut zu überwachen, dass die hochsensible Elektronik schnell erkennt, wenn etwas nicht mehr rund läuft.
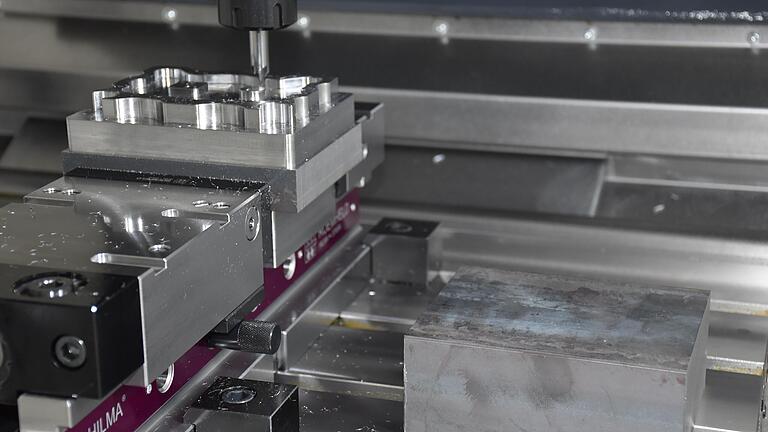
Diese Überwachung von Maschinen und Anlagen hat viele Gesichter. So kann etwa der Stromfluss in einer Maschine Aufschluss über deren Zustand und damit über drohende Ausfälle geben. Als "Fischertechnik-Lernfabrik" war dazu eine Förderbandanlage aus den eigentlich als technisches Spielzeug gedachten Komponenten im Miniaturformat nachgebaut. In der kleinen Anlage wurden Störungen simuliert und gezeigt, was passiert, wenn Verschleißteile an einer solchen Anlage ausfallen. Die Überwachung funktioniert im kleinen wie im Großen. Betriebe können durch die Auswertung des Stromprofils ihrer Anlagen erkennen, ob sich zum Beispiel etwas verklemmt hat oder ob andere Gründe vorliegen, weswegen das Band nicht mehr optimal läuft.
Die Bewegungssensorik an einem Akkuschrauber, der an einem Montageband von einer Arbeitskraft bedient wird, ermöglicht die Beobachtung der Arbeitsabläufe in Echtzeit. Das diene keinesfalls dazu, die Arbeitsleistung zu überwachen, so Florian Grabi, sondern ermögliche, Ursachen für Prozesszeitschwankungen aufzudecken und Optimierungspotenziale in der Montage zu erschließen. Grabi hat gemeinsam mit Julian Meier und Cuk Emir ein drahtloses Sensorsystem für die Überwachung der Werkzeuge in der manuellen Montage entwickelt. Nach dem Motto "Kleine Ursache, große Wirkung", könnten dabei auch Kleinigkeiten, wie eine falsche Positionierung der Werkzeuge im Montageprozess aufgedeckt werden.
An den Maschinen "horchen" heißt Fehler früher erkennen
Das Geräusch, das zum Beispiel ein Fräskopf beim Bearbeiten eines Werkstückes macht, lässt Rückschlüsse auf dessen Verschleiß zu. Techniker Wolfgang Schmitt demonstrierte die KI-gestützte Suche nach Hinweisen auf Verschleiß an Werkzeugmaschinen. Signalmuster werden akustisch analysiert, so wird frühzeitig und noch bevor die Fachkraft an der Maschine dies hören kann, erkannt, wenn etwa der Fräskopf ausgetauscht werden muss.
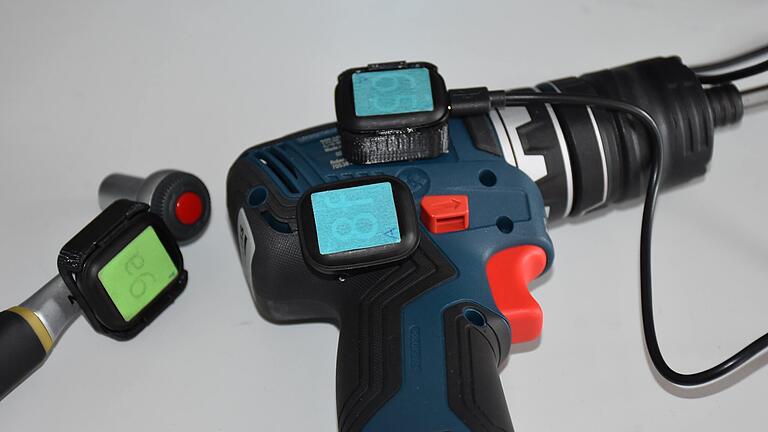
Weniger ungeplanter Stillstand, höhere Standzeiten der Werkzeuge, bedarfsgerechte Wartung und höhere Ressourceneffizienz sind die Vorteile für die Betriebe. Das zahlt sich finanziell aus, denn wird ein Werkzeug zu früh gewechselt, verursacht dies Kosten, wird es zu spät gewechselt, drohen unbrauchbare Werkstücke und Ausfallzeiten, so Techniker Wolfgang Schmitt, der dies anhand einer Fräsmaschine demonstrierte.
Optimierung zahlt sich für die Betriebe in barer Münze aus
In all diesen Fällen sei die sensorische Überwachung industrieller Fertigungsprozesse auch eine Hilfestellung für die Menschen, die an den Anlagen stehen oder die Maschinen bedienen. "Was erfahrene Mitarbeiter vielleicht hören, überhören vielleicht jene, die noch nicht so lange an der Maschine stehen", so Christoph Hoffmann. Die zusätzliche Überwachung sorge auch für zusätzliche Sicherheit, weil sie Verschleiß-Prognosen erstellt und vorausschauende Wartungsempfehlungen gibt.
Neben all diesen und weiteren innovativen elektronischen Möglichkeiten, Fehlern in Produktionsabläufen auf die Spur zu kommen, stellte auch die FHWS ein interessantes Projekt vor. PlanAR (AR steht für Augmented Reality) ist ein gefördertes Projekt und beschäftigt sich mit dem Einsatz von AR bei Anlagenplanung und Materialflussoptimierung. Produktionsabläufe werden virtualisiert, selbst bei der Planung von Fertigungsanlagen kann diese Technik helfen, wie der wissenschaftliche Mitarbeiter de FHWS, Maximilian Rosilius, einem interessierten Publikum erläuterte.