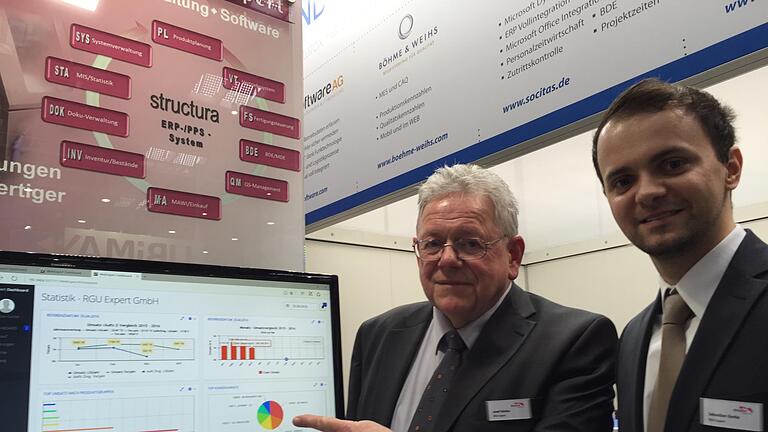
Das kennt man von der Hannover Messe: überall neunmalkluge Roboter, Maschinen als Alleskönner und jede Menge Manager mit Krawatten und feinem Zwirn. Doch man muss weg von diesen Standardbildern und genau hinschauen, will man in die Tiefen des Leitthemas der diesjährigen Schau eindringen: Industrie 4.0.
Ein Thema, das es schon seit fünf Jahren gibt. Aber heuer wird es auf der weltgrößten Industriemesse und in den Fachmedien wie die sprichwörtliche Sau durchs Dorf getrieben. Der Rummel um die auch als vierte industrielle Revolution bezeichnete Welle kommt nicht von ungefähr: Industrie 4.0 ist auf gutem Weg, unseren Arbeitsalltag und damit ein Stück unseres Lebens auf den Kopf zu stellen.
Es geht um tief greifende Veränderungen etwa in Fabriken. Kaum ein Aussteller auf der Hannover Messe, der nicht zeigt, dass an der Werkbank, in der Wartung, im Lager oder im Vertrieb künftig Daten an allen möglichen Stellen erfasst werden.
Der Clou an der Sache: Die Daten dienen zum Beispiel dazu, dass eine Maschine selbst „weiß“, wann und vor allem wo genau sie kaputt gehen wird. Predictive Maintainance heißt das.
Freilich ist in Fachkreisen unstrittig, dass die Auslagerung von Firmendaten in die berühmte Datenwolke (Cloud) – eines der wesentlichen Elemente von Industrie 4.0 – eine heikle Sache ist: Wer etwa ständig Fehlermeldungen seiner Anlagen preisgibt, verrät der Konkurrenz unter Umständen, in welch marodem Zustand sein Maschinenpark ist.
Kein Wunder, dass auch diese Aspekte Teil der Hannover Messe sind. So befassen sich Vorträge damit, welche digitalen Angriffswege es in die Unternehmen gebe oder warum Software-Kompetenz bei Industrie 4.0 Schlüsseldisziplin sei.
Beispiel: Schaeffler aus Schweinfurt
Unter den insgesamt 5200 Ausstellern aus aller Welt sind auch gut 100 aus Franken. Und darunter wiederum die Schaeffler AG (Herzogenaurach/Schweinfurt). Auch sie ist auf der Messe in das Thema Industrie 4.0 eingestiegen.
Das Unternehmen zeigt, wie mit Hilfe von Sensoren in Schaeffler-Wälzlagern permanent Daten wie Drehmoment, Drehzahl und Temperatur erfasst werden. Mit diesen Daten wird deutlich, ob die Teile rundlaufen. Tun sie es nicht, gibt es eine Fehlermeldung.
Das Wälzlager überwacht sich also selbst. Die erfassten Daten landen in der Cloud. Dort können sie auch von außen abgegriffen werden. Mit Hilfe dieser Art von Instandhaltung „können wir Reparaturen planbarer machen“, sagte Schaeffler-Sprecher Martin Adelhardt auf der Schau.
Beispiel: Bosch Rexroth aus Lohr
Bis Freitag dauert die Hannover Messe noch. Und bis dahin zeigt auch die Bosch Rexroth AG, welche Vorteile sie in der vernetzten Industrie sieht. Das Unternehmen mit Sitz in Lohr hat eine Modellanlage aufgebaut. Schlagworte: Vernetzung, offene Schnittstellen und cloud-basierte Industrie 4.0-Lösungen in Echtzeit.
Bosch Rexroth bietet sich anderen Unternehmen an, ihnen bei der Umsetzung von Industrie 4.0 zu helfen. Einer der Ansätze: Verschleiß erkennen, bevor er zu einem Stillstand führt. Mit Hilfe von Bosch-Software sollen alle Betriebszustände in einem Fremdwerk erfasst werden.
Diese Daten werden nach Firmenangaben in die Bosch-Cloud gelegt, wo sie ein spezielles Programm auswertet. Damit soll gerade bei Großanlagen wie Stahlwerke oder Offshore-Windanlagen, wo Pannen sehr schnell sehr teuer werden, Ausfällen besser vorgebeugt werden können.
Bosch Rexroth stellte auf der Messe auch Geschäftszahlen von 2015 vor.
In eine ähnliche Richtung geht das, was die Würzburger RGU Expert GmbH auf der Messe anpreist: Eine Software für Gießereien, die einen gesamten Produktionsprozess vom Einkauf über Fertigung bis Vertrieb überwacht. Der Gießerei-Kunde könne sich via Internet und damit von jedem Ort der Welt in dieses Programm einklinken, um zu sehen, in welchem Fertigungsgrad sein Produkt ist, erklärte RGU-Berater Josef Köstler.
Beispiel: Wittenstein aus Harthausen
Die Produkte sagen den Maschinen, was sie tun müssen, die Maschinen erfassen ihre Daten selbst, die Daten stehen dem gesamten Produktionsprozess sowie je nach Bedarf auch Externen zur Verfügung: Bei Industrie 4.0 wird klar, dass nicht mehr die Handgriffe des Arbeiters das Entscheidende sind. Die neue Währung heißt: Daten.
Insofern verwundert es auf der Hannover Messe nicht, dass dort Unternehmen als Datenverwalter auftreten, die man bisher mit Werkbank, Arbeiterschweiß und Metallgeruch in Verbindung gebracht hat. So auch die Wittenstein AG.
Die als Hersteller von Antriebssystemen zum Beispiel für Raumfahrt, Formel 1 und Medizintechnik bekannt gewordene Adresse in Harthausen (Main-Tauber-Kreis) tritt in Hannover als Software-Anbieter auf: Mit dem hauseigenen Programm cymex 5 spare ein Konstrukteur von Antrieben etwa 60 Prozent Zeit bei seinen Berechnungen. Das Programm greife unter anderem auf die Daten von 14 000 Motorvarianten und von mehr als 50 Herstellern zurück, um dem Anwender bei seinen Plänen den besten Weg zu ebnen.
Beispiel: Mozys aus Würzburg
Längst spielen nicht nur die Großen bei Industrie 4.0 mit. Auch Start-Ups, also innovative Kleinunternehmen, wollen was von dem Kuchen abhaben. So die Mozys Engineering GmbH aus Würzburg. Amin Mozaffarin (37) und sein Geschäftspartner Nils Zottmann (26) haben eine kleine Box samt Sensoren und Programm entwickelt, um vor allem Schwingungen an neuralgischen Punkten einer Maschine zu messen.
Die Daten werden auf einem Bildschirm gezeigt. Dort sieht man dann, ob und wo die Maschine ein Problem hat. Via Internet könne zum Beispiel der Firmenmitarbeiter auch von zu Hause aus die Daten kontrollieren.
Und diese Daten können, wen wundert's, in die Cloud gelegt und mit anderen Daten vernetzt werden. Das mit EU- und Bundesgeldern geförderte Jungunternehmen gibt es seit Mitte 2015 und hat seinen Sitz im Innovations- und Gründerzentrum in Würzburg. Noch warten Mozaffarin und Zottmann auf den Durchbruch – aber den bringe ja vielleicht die Hannover Messe.
Wichtige Begriffe zu Industrie 4.0
- Smart Factory: „Intelligente Fabrik“, in der Maschinen und Produkte ohne Eingriff des Menschen und ohne (Personal-)Computer selbst miteinander kommunizieren („Internet der Dinge“). Grundlage dafür ist eine Vernetzung aller produktionsrelevanten Daten auch nach draußen – das Herzstück von Industrie 4.0.
- Predictive Maintenance: „Vorausschauende Instandhaltung“, was bedeutet: Teile einer Maschine sagen anhand permanent per Sensoren gesammelter Daten selbst voraus, in welchem Zustand sie sind und wann sie kaputt gehen werden.
- Condition Monitoring: „Zustandsüberwachung“, also das ständige Sammeln von Daten rund um eine Maschine (zum Beispiel Schwingungen, Temperatur, Position), um ihre Leistungsfähigkeit im Auge zu behalten und Ausfälle rechtzeitig erkennen zu können. Wesentlicher Teil von Predictive Maintenance.
- Additive Fertigung: Klassisches Instrument dafür ist der 3D-Druck anhand von Computerdaten. Additive Fertigung wird oft eingesetzt, um Modelle für die Serienproduktion oder um Werkzeuge herzustellen.
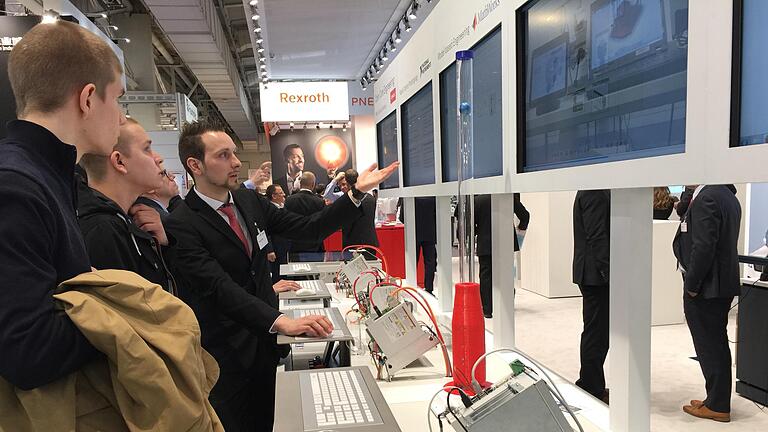
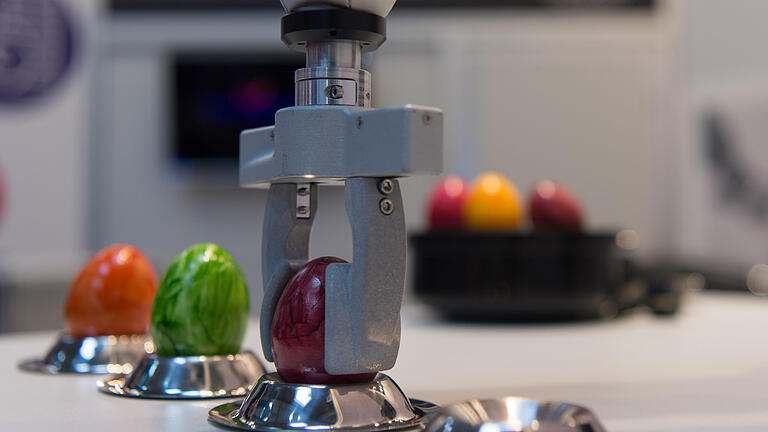
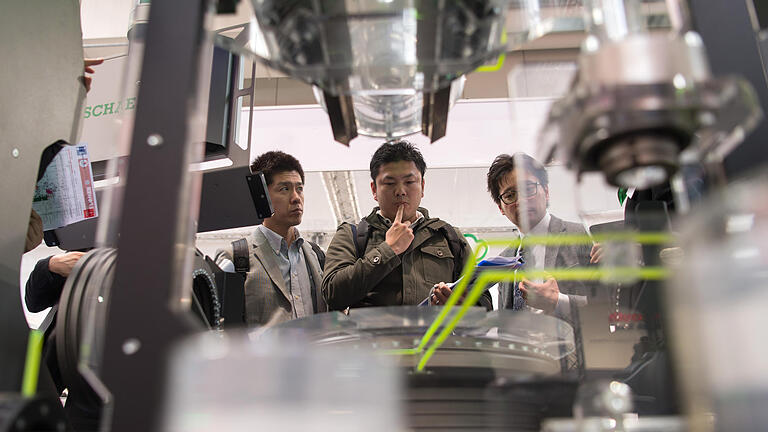