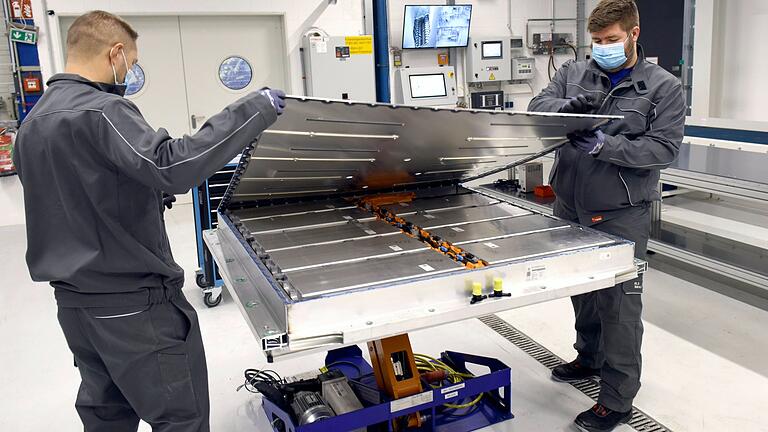
Nach Tesla setzt jetzt auch Volkswagen auf die Produktion eigener Batterien für Elektroautos. Und in einem Punkt ist VW dem Konkurrenten offenbar einen Schritt voraus: beim Recycling solcher Akkus.
Möglich macht's ein Unternehmen aus Karlstadt (Lkr. Main-Spessart): die URT Umwelt- und Recyclingtechnik GmbH. "Wir sind der weltweit der erste Anlagenbauer, der eine funktionierende Anlage bei einem Autohersteller in Betrieb hat", sagt Peter Heßler, einer der beiden Geschäftsführer. Es handelt sich zunächst um eine Pilotanlage in Salzgitter.
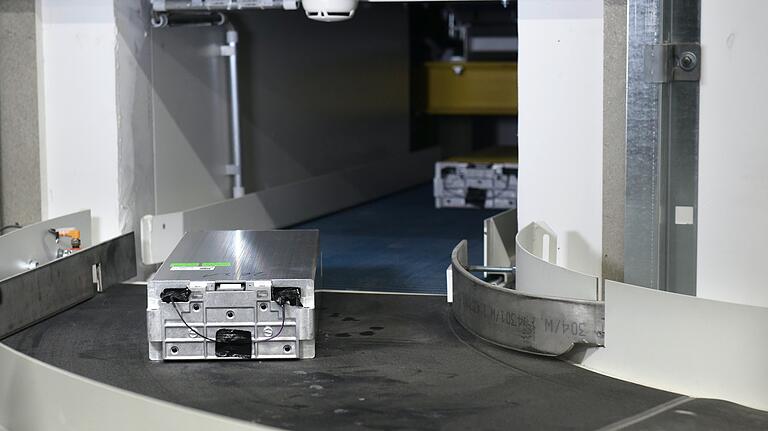
2020 machten die Kosten für die Batterie laut Statista 38 Prozent des Anschaffungspreises eines Elektroautos aus. Die Autobauer suchen daher nach Wegen, um diese Kosten zu verringern. Nicht nur deshalb ist die Wiederverwertung von Batterien wichtig.
Ein Makel der Batterieproduktion sind die oftmals fragwürdigen Bedingungen, unter denen die Rohstoffe wie Kobalt oder Lithium gewonnen werden – teilweise mit Kinderarbeit, unter gefährlichen Umständen und verbunden mit immensen Umweltschäden. Da drängt sich der sorgsame Umgang mit diesen Rohstoffen auf. Dennoch ist VW laut Heßler der erste Autobauer, der sich intensiv mit dem Recycling der Batterien beschäftigt.
Erst weiterverwenden, dann recyceln
Im Auto halten Batterien rund acht Jahre. Haben sie ausgedient, werden sie nach dem Konzept von Volkswagen bei der Rücknahme zunächst analysiert. Liegt die Leistungsfähigkeit noch bei 80 Prozent, können die Module zunächst noch weiterverwendet werden, beispielsweise in Schnellladesäulen oder in Hausspeichern für Solarstrom. Sind irgendwann nur noch 70 Prozent erreicht, kommt es zum Recycling.
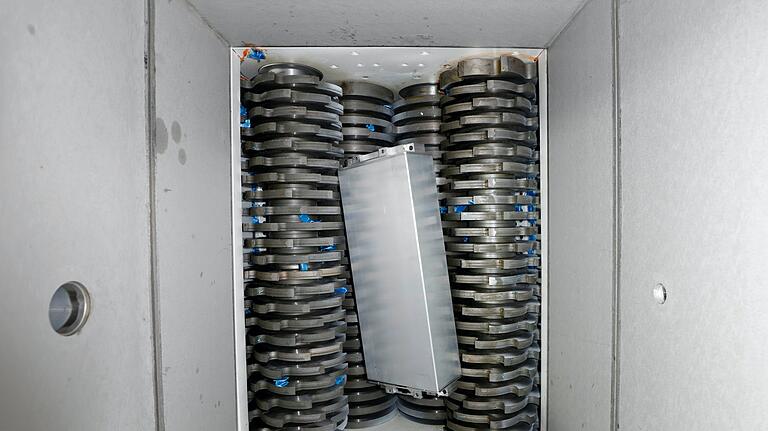
Eine Batterieeinheit besteht aus Modulen, die wiederum Zellen enthalten. Vor dem Recycling wird die Batterie zunächst entladen und demontiert. Sind Kabel, Aluminiumgehäuse und andere Bestandteile entfernt, wandern die schuhkartongroßen Module in die Recyclinganlage. Dort werden sie stark zerkleinert.
Da dabei der flüssige Elektrolyt mit den festen Stoffen vermischt wird, muss das entstehende Gemisch getrocknet werden. Dabei wird der Elektrolyt – zum größten Teil bestehend aus Kohlenwasserstoffen – zurückgewonnen. Heßler: "Die Korngröße von 15 Millimetern ist optimal, um nach der Trocknung das sogenannte Schwarze Pulver durch Sieben von anderen Fraktionen zu trennen."
"Schwarzes Pulver" für Kathoden und Anoden
Das Schwarze Pulver enthält unter anderem Lithium, Mangan, Kobalt, Nickel und Graphit. Die Metalle Kobalt und Lithium, aber auch Mangan und Nickel dienen je nach Batterietyp zur Herstellung neuen Kathodenmaterials. Graphit wird für das Anodenmaterial benötigt. Getrennt werden diese Stoffe in weiteren physikalischen und chemischen Prozessen. Beim Recycling wird über einen Magneten noch Eisen abgeschieden. Aluminium, Kupfer und Kunststoff werden separiert.
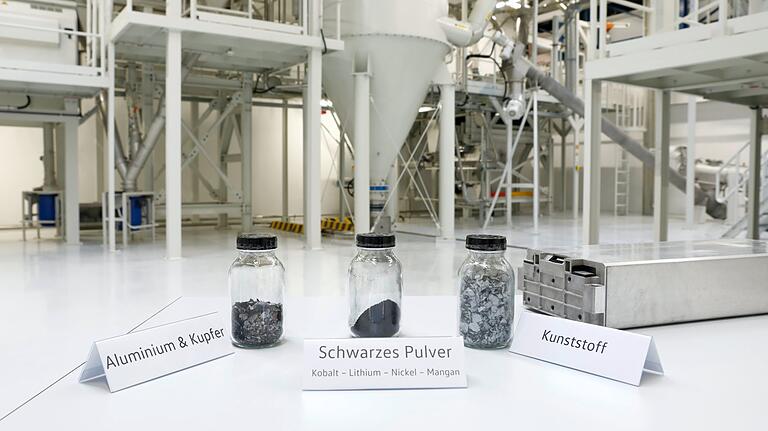
Die Karlstadter URT beschäftigt sich schon seit 2012 mit der Aufbereitung von Lithium-Ionen-Akkus und baute 2014 einen kleinen Prototypen für ein deutsches Forschungsvorhaben. Das Unternehmen bringt für die Konstruktion solcher Anlagen optimale Voraussetzungen mit. Bei der Gründung 1995 lag der Schwerpunkt auf Schreddermaschinen mit rotierenden Scherwellen, wie sie jetzt auch zum Zerkleinern der Batteriemodule verwendet werden.
URT nutzt seine Erfahrungen
Bahnbrechend war für URT die Entwicklung von Recyclingstraßen für Kühlgeräte, bei denen während des Durchlaufens das klimaschädliche FCKW abgesaugt wird. Elemente dieser Technik kamen auch jetzt wieder zum Einsatz, als es darum ging, die Zerkleinerungsschritte gasdicht gekapselt ablaufen zu lassen. Überdies ist beim Zerkleinern von Autobatterien auf eine inerte Atmosphäre – also mit weniger als fünf Prozent Sauerstoff – zu achten, damit es nicht zu Bränden kommt.
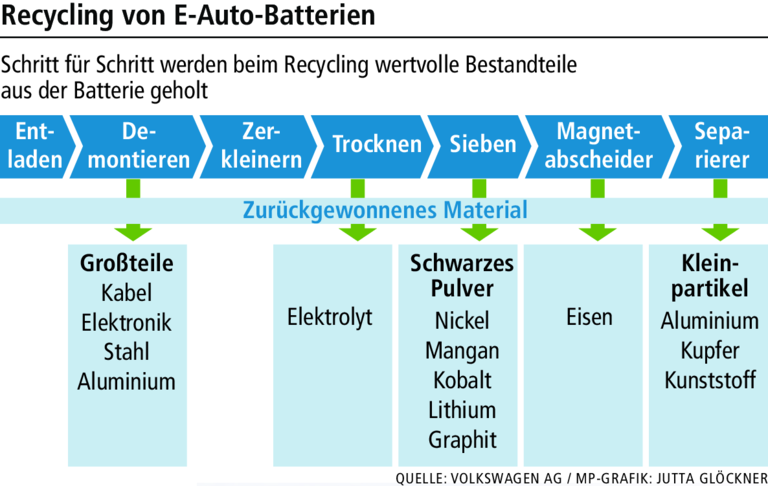
Mehr als 90 Prozent des Batteriematerials können mit der Technik von URT wiedergewonnen werden. Pro neuer 62 kWh-Batterie werden 1,3 Tonnen CO2 eingespart, wenn für Kathoden 100 Prozent wiederverwertete Rohstoffe und Grünstrom genutzt werden, betont Volkswagen. Die Pilotanlage in Salzgitter kann pro Stunde rund 150 Kilogramm Batteriemodule schlucken. Geplant sind Anlagen mit bis zu vier Tonnen pro Stunde. Inzwischen freut sich URT über Kontakte zu Batterieherstellern weltweit.