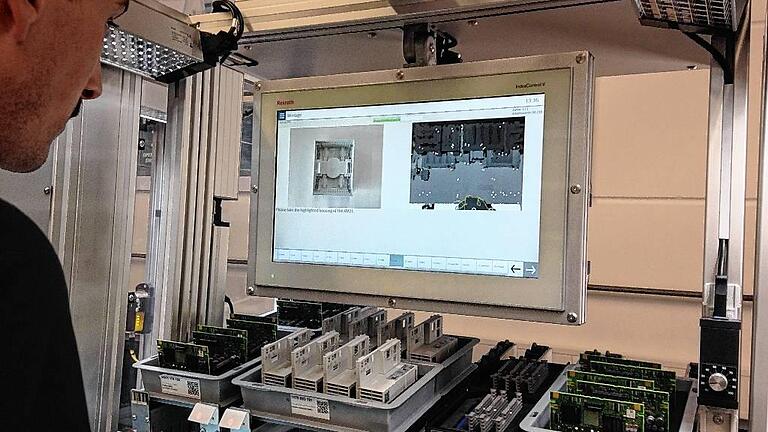
Höllenhammer. Der Name der ersten Fertigungsstätte der Familie Rexroth gibt einen Eindruck davon, wie es dort zuging: laut und heiß. Der Main-Zufluss Elsava trieb den Schmiedehammer an – Produktion in der Industrie 1.0, in der man Wasserkraft oder Dampf nutzte. 221 Jahre später steht Mark Leverköhne in einer Bosch-Rexroth-Fertigungshalle in Lohr (Lkr. Main-Spessart). Sie ist Teil des Werks LoP2 – das klingt weniger martialisch als Höllenhammer, die Fabrik steht für die Fertigung in der Industrie 4.0. Leverköhne ist stellvertretender Leiter des Werks, durch das er an einem Praxistag Besucher führt.
Bosch-Rexroth, das zuletzt vor allem wegen bevorstehender Entlassungen in seiner Gießerei in den Fokus der Öffentlichkeit rückte, möchte bei einem Fabrikrundgang zeigen, wie es seine Produktion vernetzt – ein Thema, das seit 2011 unter dem Schlagwort „Industrie 4.0“ diskutiert wird. In dem Werk werden „Herz, Muskeln und Hirn“ für Maschinen hergestellt, wie Leverköhne beschreibt – Bosch-Rexroth fertigt hier Antriebs- und Steuerungstechnik.
Das besondere an dem Werk: Es gilt dem Lohrer Unternehmen als Beispiel für eine „vernetzte Fabrik“. Wenn ein Kunde ein Produkt, etwa einen Servomotor für eine seiner Maschinen bestellt, wird automatisch ein Auftrag generiert. Zu Beginn des Fertigungsprozesses geschehen zwei Dinge: Jedes Teil bekommt einen „digitalen Zwilling“ zur Seite gestellt. An diesem virtuellen Produkt lassen sich alle Eigenschaften ablesen, die auch das Produkt hat: Um welche Variante handelt es sich, welche Einzelteile sind verbaut, welche Firmware ist aufgespielt?
Produkt spricht mit Maschine
Die reale Produktion beginnt mit einem Barcode: Er wird auf das Produkt geklebt und stellt die Verbindung zum digitalen Zwilling her – mit einem Scanner können die Arbeiter jederzeit ablesen, um welches Produkt es sich handelt. Gleichzeitig erlaubt der Code es dem Produkt, mit den Maschinen zu kommunizieren. Er teilt etwa mit, wo die nächste Schraube gesetzt werden soll. Diese Information kann er einer Maschine mitteilen – oder einem Menschen.
An Arbeitsplätzen in der Fabrik zeigt ein Bildschirm, welcher Arbeitsschritt als nächstes ansteht, ein Licht leuchtet über der Schraubenschachtel auf, in die ein Arbeiter greifen muss. Katharina Kern, Produktmanagerin bei Bosch-Rexroth, erklärt: „Das Produkt erzählt, was getan werden muss.“ Solche Lösungen, sagt Leverköhne, seien vor allem wichtig, wenn in einer Fabrik viele Produktvarianten hergestellt werden – etwa 200 000 sind es in Lohr.
Steffen Winkler, Leiter des Marktsegments Fabrikautomation, zeigt ein weiteres Beispiel für Industrie-4.0-Technologie: einen Akkuschrauber. Der unterscheidet sich auf den ersten Blick nur durch ein Display von einem herkömmlichen Modell, verfügt aber über eine W-Lan Verbindung. Wenn zum Beispiel in einem Flugzeug angezogene Schrauben dokumentiert werden müssen, sendet der Akkuschrauber die Daten über jede Verschraubung an das Netzwerk des Flugzeugbauers.
Damit Maschinen so miteinander kommunizieren können, müssen Standards geschaffen werden – vor allem wenn Geräte unterschiedlicher Hersteller in einer Fabrik oder über Unternehmensgrenzen hinweg miteinander kommunizieren können. Steffen Haack, Leiter des Produktbereichs Industrieanwendungen erklärt: „Die Kommunikation ist Voraussetzung der Vernetzung. Dazu braucht es Normen.“ Die sind für ein Unternehmen wie Bosch-Rexroth besonders wichtig: Die Lohrer setzen Industrie-4.0-Technologien nicht nur selbst ein, sondern statten auch Kunden damit aus.
Haack zieht den Vergleich mit einem USB-Anschluss, mit dem sich Geräte herstellerunabhängig verbinden lassen. „In der Automationstechnik sind wir davon meilenweit entfernt.“ Trotzdem gibt es inzwischen Normen, zahlreiche Verbände und Arbeitsgruppen sind daran beteiligt. Als Vorreiter sieht Haack dabei den Elektronikbereich, Hydraulik und Mechanik müssten folgen.
Der Mensch im Mittelpunkt?
Auch wenn Unternehmensvertreter beim Praxistag gerne betonen, dass „der Mensch weiterhin im Mittelpunkt“ stehe, wirft die Fertigung in der Industrie 4.0 auch die Frage auf, wie viele Menschen künftig noch in diesem Mittelpunkt stehen. Wenn Winkler etwa von einem chinesischen Hersteller erzählt, den Bosch-Rexroth ausgestattet hat – „die waren vorher vielleicht Industrie 1.5“ – berichtet er von Einsparungen von „50 Prozent bei der Manpower“. Dass die Fabrik nicht auf noch mehr als jeden zweiten Arbeitsplatz verzichten kann, liege nur am speziellen Fall.
Auch die Mitarbeiter und ihre Leistung könnten in einer vernetzten Fabrik engmaschiger kontrolliert werden. Hier sei man aber in Deutschland noch zurückhaltend, wie Produktmanagerin Kern erklärt – zu sensibel sei das Thema aus Datenschutzsicht.