Die Vielfalt an Automodellen hat enorm zugenommen. Beispiel Volkswagen: 1950 produzierte das Wolfburger Unternehmen gerade einmal zwei Baureihen: Käfer und Bulli. 1990 waren es bereits zehn Baureihen, heute laufen rund 20 verschiedene Modelle von den Bändern. Rechnet man alle zwölf Marken der VW-Gruppe mit ein, kommt man inklusive Lkw, Bussen und Motorrädern auf rund 300 Modelle. Vorbei also die Zeiten, in denen ein Werk über Jahre das immer gleiche Auto baute. Der Trend geht zu häufigen Modellwechseln und kleinen Stückzahlen. Eine Autofabrik mit einer einzigen Produktionslinie, die sich für mehrere Modelle eignet – so sieht die Zukunft aus. „Dafür muss die Produktion flexibler werden, dafür sind mehr Roboter und eine höhere Digitalisierung nötig“, sagt Andreas Nüchter, Informatikprofessor an der Universität Würzburg. Laserscanner sind sein Spezialgebiet. Normalerweise montiert Nüchter sie auf Roboter, in einem Projekt mit Volkswagen schickte sein Team die Sensoren jetzt aber durch Autofabriken. Im Interview erklärt der Informatiker, warum.
Frage: Professor Nüchter, Sie haben einen Scanner 3-D-Bilder von VW-Fabriken aufnehmen lassen. Wieso?
Prof. Andreas Nüchter: Bevor ein neues Automodell vom Band läuft, muss der Hersteller herausfinden, ob das neue Modell nicht irgendwo in der Fabrik anecken würde. Bei Volkswagen gibt es eine konzerneinheitliche Aufhängung, auf der die Fahrzeuge durch die Fertigungsstraße fahren. Darauf haben wir unsere Sensorik gesetzt, in diesem Fall ein Laserscanner. Diese Laser setzen wir sonst an mobilen Robotern ein. Jetzt haben wir den Roboter weggelassen und den Laser sozusagen auf das Förderband gesetzt.
Was macht der Laser?
Nüchter: Mit dieser Sensorik können wir Fertigungsanlagen abfahren und dreidimensional vermessen. Der Clou dabei ist: Wir kriegen diese Anlage genau aus der Sicht des zu montierenden Fahrzeugs. Wir kennen also nicht nur die Geometrie der Anlage, sondern wissen auch genau, wie sich das Fahrzeug durch die Halle bewegen würde. In der Simulation setzen wir dann das neue Fahrzeugmodell in die virtuelle Halle und gucken: Passt das denn überhaupt noch durch?
Wieso sind diese Messungen notwendig? Kennt VW seine Fabriken nicht?
Nüchter: Da kann man jetzt natürlich sagen: Haben die keine Pläne von der Werkhalle? Aber die sind nie aktuell. Bei Volkswagen zum Beispiel treffen sich die Teams, die die Autos zusammenschrauben, regelmäßig und überlegen, was sie besser machen könnten. Wenn dann zum Beispiel ein Mitarbeiter eine Lampe haben möchte, um besser zu sehen, wo er die Schraube setzen kann, dann bekommt er die Lampe. So etwas wird aber nicht in irgendwelchen Plänen festgehalten. Deswegen ist es notwendig, die Hallen zu vermessen.
Wie hat man Zusammenstöße in der Autofabrik bis jetzt verhindert?
Nüchter: Da gibt es mehrere Möglichkeiten. Autos werden in der Regel größer. Der Golf I hat nichts mehr mit dem Golf VII zu tun. Also nimmt man ein altes Auto und modelliert mit Styropor ungefähr das neue Auto. Man klebt Styropor an die alte Karosserie, schickt den Wagen durch die Fertigungshalle und guckt, wo er hängen bleibt. Die ersten Autos, die produziert werden, werden auch nicht verkauft, weil die dann doch mal anschlagen.
Und Ihre Methode ist so genau, dass das nicht mehr notwendig ist?
Nüchter: Genau, oder zumindest seltener notwendig. Und vor allem wird damit sehr viel Zeit gespart. Statt ein Team das Auto in Styropor modellieren zu lassen, es durch die Fabrik zu schicken und zu analysieren, wo es anstößt, schicken wir unsere Sensorik einmal durch die Fabrik und haben das Ergebnis sofort.
Wo waren ihre Scanner im Einsatz?
Nüchter: Wir haben Fertigungsanlagen am Stammwerk in Wolfsburg und im Werk in Hannover abgebildet und dabei den Crafter und den Tiguan modelliert.
Heute bauen Hersteller mehr Modelle in kürzeren Zyklen. Ist das Problem dadurch akut geworden?
Nüchter: Genau. 1950 produzierte Volkswagen drei Typen: den guten alten Käfer, den Bulli und den Karmann-Ghia. 1990 gab es zehn. Jetzt sind sie bei 17 Typen. Wenn man sich das auf Konzernebene ansieht, kommt man auf 280 verschiedene Typen. Auch die Modellwechsel geschehen häufiger. Früher gab es etwa alle vier Jahre einen Wechsel, jetzt geht der Trend zu Zyklen von zwei Jahren. Und dann das große Stichwort Industrie 4.0. Das heißt, es werden kleinere Serien gebaut, es wird häufiger gewechselt. Eventuell kommen wir auch später mal dahin, ganz individuell Autos zu konfigurieren. Industrie 4.0 bedeutet irgendwann eventuell eine Losgröße von eins.
Was war die größte Herausforderung bei dem Projekt?
Nüchter: Die Präzision. Volkswagen hat Genauigkeitsanforderung, die sehr schwierig zu erfüllen ist. Diese Sorte Laserscanner ist typischerweise zwei bis drei Millimeter genau. Die Rekonstruktion der Gesamtumgebung musste ähnlich genau werden, damit die Daten für die Produktion eingesetzt werden können.
Mit Laserscannern setzen Sie sich schon lange auseinander. Wo bringen Sie die Geräte noch zum Einsatz?
Nüchter: Überall, wo mobile Roboter eine Umgebung kartieren sollen. Wir träumen natürlich alle vom Mars- und Mondroboter. Die Wahrscheinlichkeit, dass wir mal einen Roboter der Uni da hochschicken, ist sehr gering. Aber es gibt auch andere Anwendungsfelder. Wir haben uns zum Beispiel schon mit der Abbildung von Erdbebengebieten beschäftigt. Aktuell arbeiten wir mit dem Zentrum für Telematik, zwei Firmen und der staatlichen Feuerwehrschule an einem Projekt, in dem wir Laserscan-Technologie auf eine Drohne bringen wollen. Damit soll die Feuerwehr dann sofort eine dreidimensionale Karte vom Einsatzort zur Verfügung haben.
Andreas Nüchter
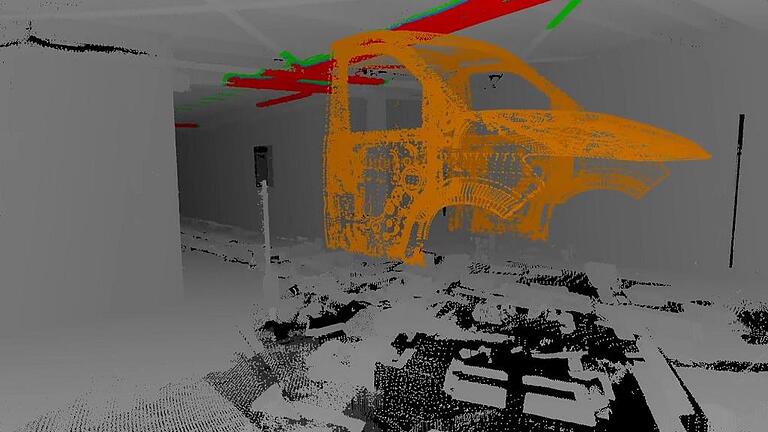
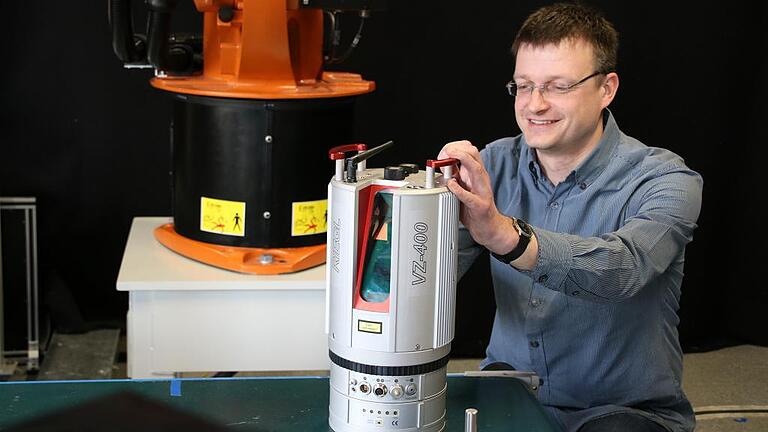