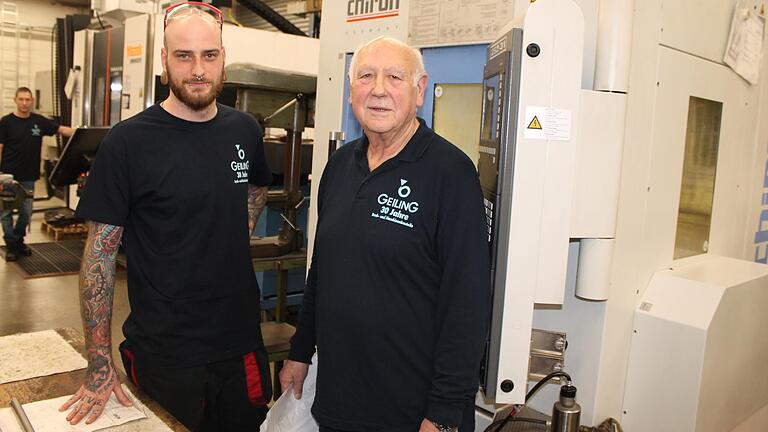
Es ist immer wieder beeindruckend, welche Erfolge und Ergebnisse man mit Mut, Fleiß, Tatkraft, einer gehörigen Portion Optimismus und mit handwerklicher Spitzenleistung erreichen kann. Ein Paradebeispiel für so eine Erfolgsgeschichte ist die Gerolzhöfer Firma Dreh- und Maschinenbauteile Geiling GmbH. Aus denkbar kleinsten Anfängen hat sich ein mittelständisches Unternehmen entwickelt, das heute national wie international einen hervorragenden Ruf genießt.
In diesen Tagen vor genau 30 Jahren hat der heute 73-jährige Rudolf Geiling seine Ein-Mann-Firma ins Leben gerufen. Die erste Produktionsstätte war die kleine Garage neben dem Wohnhaus, das Rudolf gemeinsam mit seiner Ehefrau Erika an der Friedrich-List-/Hans-Böckler-Straße baute. Und vor zehn Jahren wurde dann die große Werkhalle am Spielsee bezogen, wo die Firma auch heute noch produziert.
Der Traum der Selbstständigkeit
Als Maschinenbaumechaniker-Meister mit sehr guten Verbindungen zur Schweinfurter Großindustrie ging Geiling schon länger mit seiner Idee schwanger, sich selbstständig zu machen, eine eigene Firma zu gründen und sich als spezialisierter Zulieferer einen Namen zu machen. In die breite Massenproduktion bei der Metallbearbeitung einzusteigen, damit hätte man auch vor 30 Jahren kein Geschäft mehr machen können. In dem Bereich waren die großen Fabriken in Schweinfurt mit ihrer exakt durchgetakteten Fließbandfertigung unschlagbar. Rudolf Geiling erkannte aber eine Nische, die Erfolg versprach: die Produktion von Dreh- und Maschinenbauteilen, die in der Industrie in nur relativ kleiner Stückzahl benötigt wurden – in solcher Stückzahl, dass sich die Herstellung in der Großindustrie kaum rechnete, weil dort die Maschinen erst immer aufwändig hätten umgerüstet werden müssen.
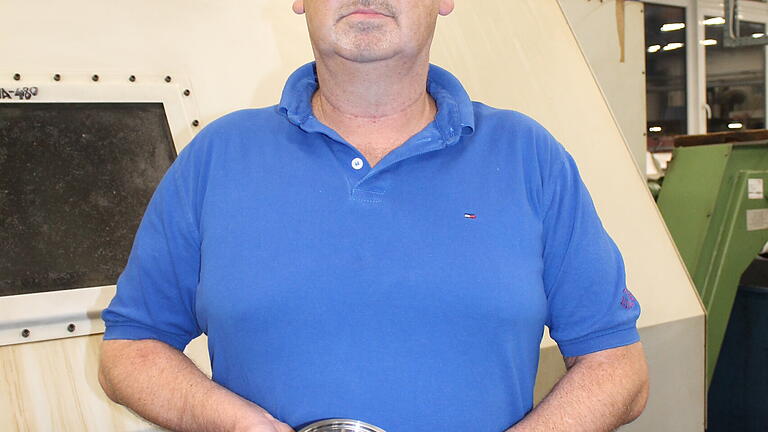
Die Nischen-Idee ging auf. Die kleine Garagen-Firma, mit großer Unterstützung seiner Ehefrau, begann ihre Erfolgsgeschichte: Noch im Gründungsjahr 1990 stellte Rudolf Geiling den ersten Mitarbeiter ein, der gemeinsam mit dem Chef an gebraucht gekauften Fertigungsmaschinen die ersten Bestellungen für zu fräsende Kleinteile herstellte. Wenig später nahm der Meister seinen ersten Auszubildenden unter seine Fittiche. Es sollte nicht der letzte sein. "25 Auszubildende haben wir seitdem schon gehabt", erzählt Geiling nicht ohne Stolz. Viele davon hat er nach dem Ende ihrer Ausbildung auch im Betrieb übernommen. Es gehört zum Erfolgsgeheimnis der Firma, dass man sich hochqualifizierte Mitarbeiter selbst heranzieht.
Die erste Werkhalle
Noch im Gründungsjahr 1990 errichtete Rudolf Geiling auf seinem Grundstück zur Hans-Böckler-Straße hin eine Werkhalle mit Büro- und Sozialräumen auf einer Fläche von 450 Quadratmetern. Der Maschinenpark vergrößerte sich und brauchte Platz. Ein Jahr später wurde das erfolgreiche Führungsduo Rudolf und Erika zum Trio: Sohn Holger Geiling trat nach seiner Ausbildung zum Maschinenbaumechaniker 1991 in den Familienbetrieb ein. 1997 legte er die Meisterprüfung im Maschinenbau ab und ist seit 2002 auch Betriebswirt des Handwerks.
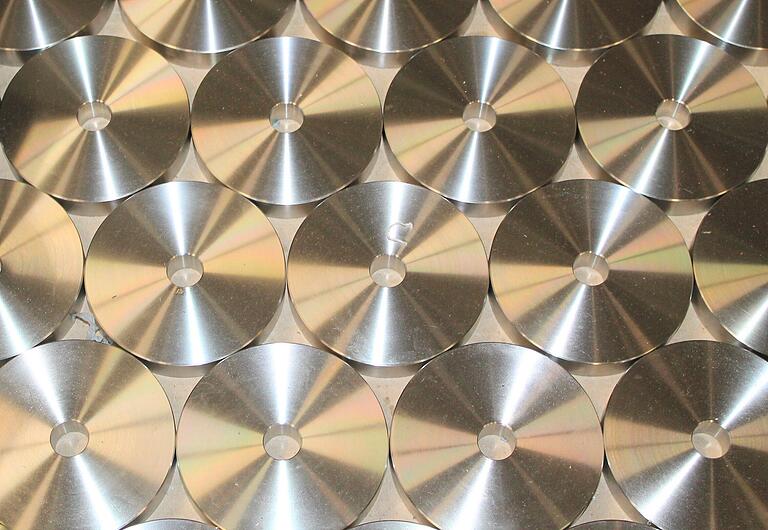
Anfang 2004 wurde die Einzelfirma in eine GmbH umgewandelt: Rudolf und Holger Geiling sind fortan Geschäftsführer mit je 50 Prozent Geschäftsanteilen. Auch für die Zukunft ist heute schon alles geplant: "Im Jahr 2022 wird mein Sohn alleiniger Gesellschafter werden", sagt Rudolf Geiling. 75 Jahre alt wird dann der Seniorchef sein. Da wird es Zeit, sich etwas mit dem Ruhestand anzufreunden.
Wechsel zum Spielsee
2008 platzte das prosperierende Familienunternehmen, das mittlerweile im Zweischicht-Betrieb produzierte, am alten Standort aus allen Nähten. "Wir mussten uns Gedanken machen, wie es weitergehen soll", erinnert sich der Firmengründer. Da tat sich just zur rechten Zeit eine "einmalige Chance" auf, wie es Rudolf Geiling bezeichnet: Die alteingesessene Spedition Vetter im Rügshöfer Gewerbegebiet stellte ihren Betrieb ein. Familie Geiling konnte von dem Speditionsgelände am "Spielsee" eine Fläche von rund 13 000 Quadratmetern kaufen. Mit dabei: das Verwaltungsgebäude mit Büro- und Sozialräumen auf rund 300 Quadratmetern und die große, ehemalige Lkw-Halle mit rund 900 Quadratmetern.
Doch nach der "einmaligen Chance" kam postwendend der Rückschlag. Der Zusammenbruch der US-amerikanischen Großbank Lehman Brothers löste eine weltweite Wirtschaftskrise aus, die Auftragslage bei Geiling verschlechterte sich dramatisch. "Wir mussten Kurzarbeit anmelden", erinnert sich Rudolf Geiling an die schwierige Phase. Gleichzeitig hat man eine zweite Entscheidung getroffen, die viel über das unternehmerische Naturell des Firmengründers aussagt: Statt Personal zu entlassen, weil die Aufträge fehlten, hat Geiling seine Leute zu Weiterbildungskursen geschickt. Als der Konjunkturmotor dann relativ schnell wieder ansprang, zahlte sich diese weise Entscheidung bald aus.
Start am neuen Standort
Vor zehn Jahren startete nach einigen Umbauarbeiten die Produktion am neuen Standort. Über 30 Mann sind hier beschäftigt. Von montags bis freitags wird in drei Schichten rund um die Uhr gearbeitet. Der Standort steht auch für die Zukunft des Unternehmens: "Wir haben noch ausreichend Platz für Erweiterungen", sagt Rudolf Geiling. Platz, der bald genutzt wird. In diesem Jahr entsteht mit einem Anbau ein neues Materiallager. Der Platz hinten in der Werkhalle, wo jetzt noch die schweren Metallvorräte liegen, wird künftig für zusätzliche Fertigungsmaschinen benötigt.
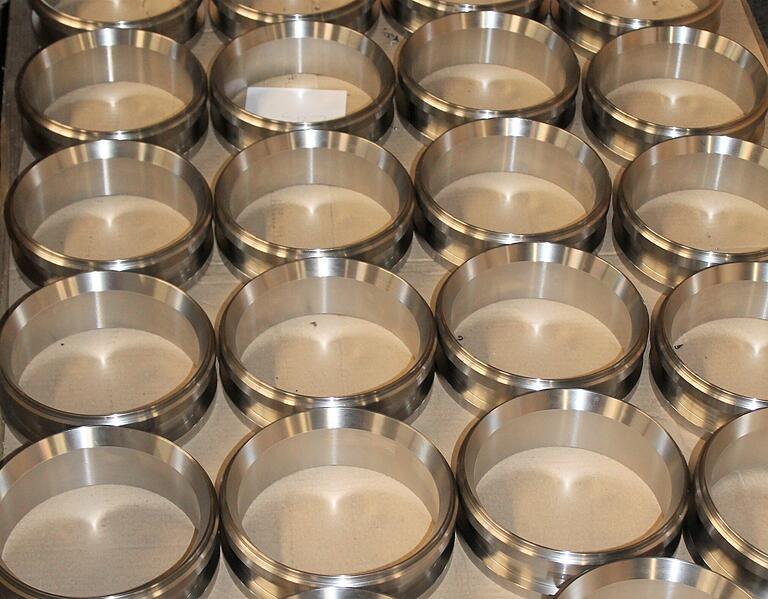
Der Kundenkreis kommt aus allen Branchen in ganz Deutschland, überwiegend aber aus Bayern. "Wir haben rund 400 Kunden in unserer Kartei", sagt der Firmengründer. Der Umsatz pro Jahr hat längst die Millionengrenze geknackt und liegt derzeit bei 2,5 Millionen Euro.
Große CNC-Maschinen
In der Werkhalle stehen die "Bearbeitungszentren", große Maschinen, die wie riesige Würfel aussehen. Durch Sichtscheiben kann man ins Innere blicken und sieht, wie unter einem stetigen Strom von kühlender Emulsion, einer Mischung aus Wasser und Spezialöl, die Metallteile bearbeitet werden. Ein Roboterarm fährt zur Seite und eine Nische öffnet sich, wo verschiedene Werkzeug-Aufsätze bereitstehen. Der Roboter holt sich dort genau das Werkzeug ab, das er zum nächsten Fertigungsschritt benötigt. Dann geht es zurück zum Werkteil und die Maschine beginnt wieder mit der Bearbeitung. In anderen CNC-Maschinen ist die Bearbeitung etwas anders gelöst: Hier sind die extra gehärteten Werkzeuge für die Stahlbearbeitung bereits schon alle auf einem zentralen "Revolver" eingespannt und dieser Revolver bringt durch Drehen das jeweils gewünschte Werkzeug an das Werkteil heran.
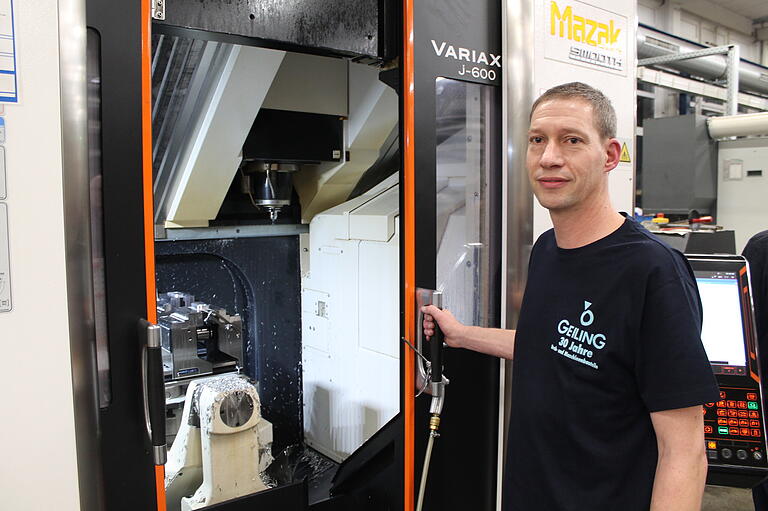
Alle Details vorprogrammiert
Verantwortlich für eines der Fünf-Achs-Fräszentren ist beispielsweise der CNC-Fräser Christian Borschert. Bevor ein bestimmtes Werkteil aus Metall oder Kunststoff im Fräszentrum hergestellt wird, wurde jeder kleinste Arbeitsschritt und die Reihenfolge dieser Arbeitsschritte exakt in der Maschine programmiert. Grundlage der Programmierung sind die Pläne, die von den jeweiligen Auftraggebern an die Firma Geiling weitergereicht werden. So eine "Computerized Numerical Control"-Maschine ist dann in der Lage, die Werkstücke mit außerordentlich hoher Präzision auch für komplexe Formen automatisch herzustellen. Borscherts Aufgabe nach der Programmierung ist es, das Werkteil in die Maschine einzuspannen, den Bearbeitungsprozess zu überwachen und am Ende das Teil wieder aus dem Fräszentrum herauszunehmen.
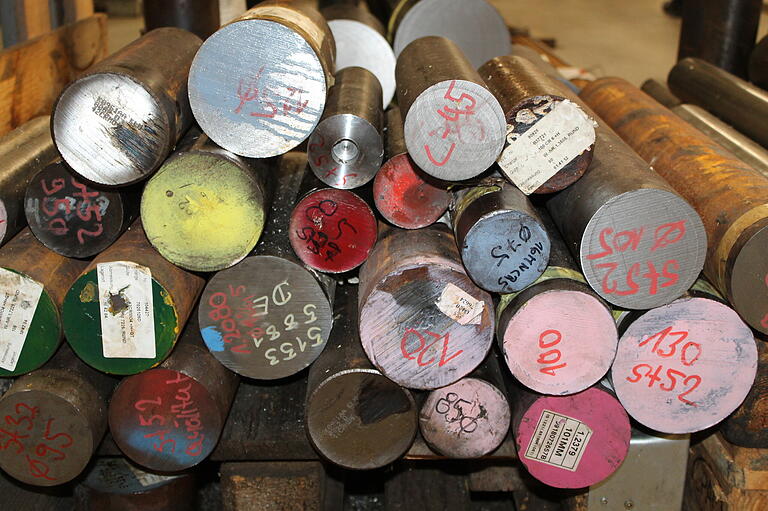
Je nach Komplexität des Vorgangs kann das Fräsen in zwei Minuten beendet sein, es kann aber auch drei- oder viermal so lange dauern. Deshalb ist es denkbar, dass ein CNC-Spezialist für zwei Fräszentren mit unterschiedlicher Bearbeitungsdauer gleichzeitig zuständig ist. Da ist es die knifflige Aufgabe der Unternehmensführung, die Produktion an beiden Maschinen so zu takten, dass der CNC-Fräser nicht an beiden Maschinen gleichzeitig gebraucht wird, sondern dass dies immer schön abwechselnd der Fall ist.
Absolute Präzision
Im Mittelpunkt aller Arbeiten steht die absolute Präzision. "Wir arbeiten beim Fräsen im Bereich von einem Hundertstel Millimeter", erklärt Holger Geiling. Noch genauer kann es sogar durch anschließendes Schleifen werden. Dieser hohe Qualitätsstandard der Firma wird durch verschiedene Zertifizierungen belegt. Dazu zählt auch, dass die Geiling GmbH bereits seit 2008 als Lieferant von Einzelteilen für die Schaeffler Aerospace GmbH zugelassen ist. Zum weltweiten Kundenstamm von Schaeffler Aerospace gehören alle namhaften Hersteller von Triebwerken von Flugzeugen, für Hubschrauber, die europäische Trägerrakete Ariane sowie für spezielle Anwendungsfelder mit hohen Leistungsanforderungen. Und so kann es also tatsächlich sein, dass ein in Gerolzhofen gefertigtes Spezialteil ins Weltall fliegt.
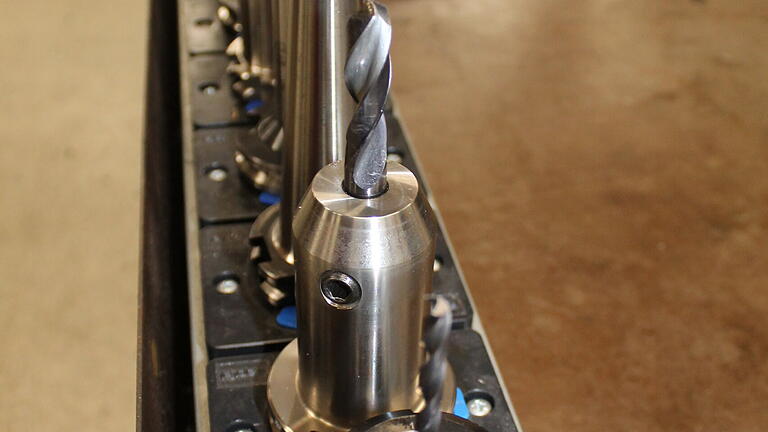
Eigenes Prüflabor
Zu den Kunden der Gerolzhöfer Firma zählen auch die Entwicklungsabteilungen großer Hersteller. "Wir werden beauftragt, Prototypen herzustellen", erzählt Holger Geiling. Erst wenn sich die Prototypen bewähren, geht die Produktion möglicherweise in Serie – heutzutage meist im osteuropäischen Ausland. Die Entwicklungsingenieure fordern für das Umsetzen ihrer neuen Ideen und Konstruktionszeichnungen eine zuverlässige und hochpräzise Arbeit – und bei den Prototypen selbstverständlich auch eine absolute Vertraulichkeit.
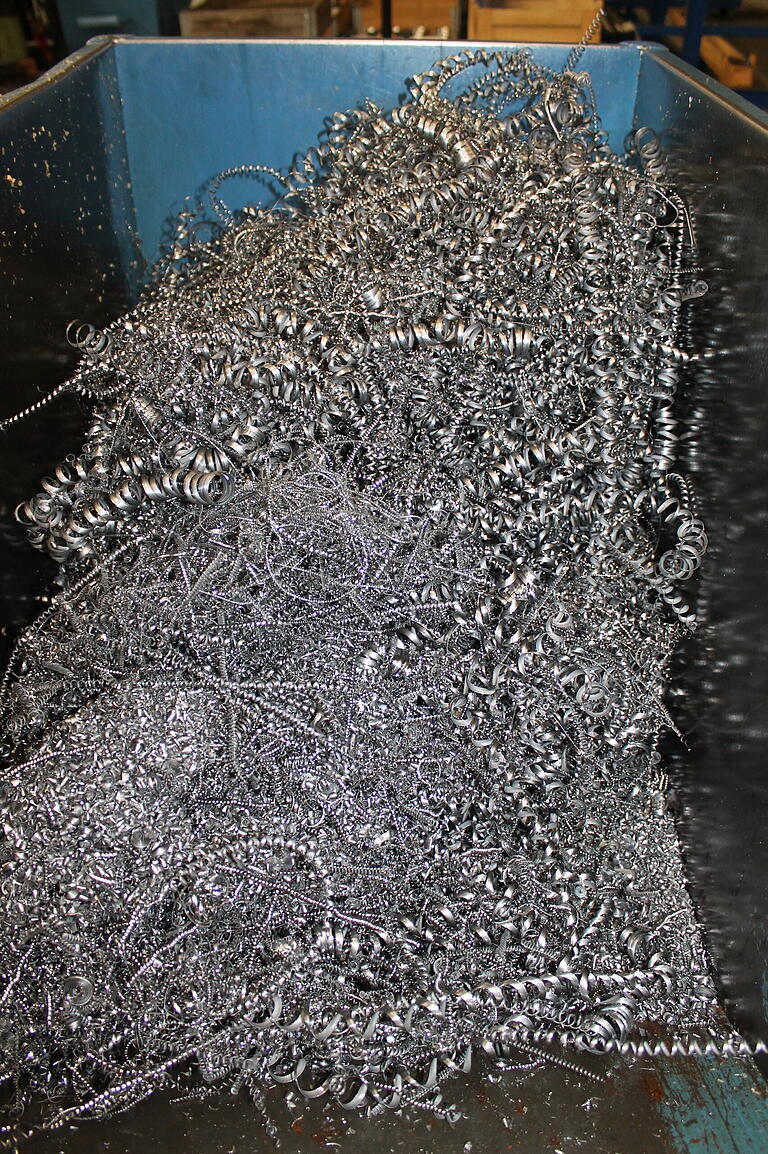
Um den eigenen Standard im Bereich der Hundertstel-Millimeter zu halten und auch zu bestätigen, unterhält die Geiling GmbH sogar ein hauseigenes Prüflabor, wo die Werkstücke regelmäßig einer Qualitätskontrolle unterzogen werden. Damit die hier gewonnenen Messwerte von den Kunden international anerkannt werden, sorgt eine Klimaanlage im Labor für eine gleichbleibende Temperatur von exakt 20 Grad Celsius. Nicht mehr und nicht weniger. Denn wäre es beim Vermessen der Werkteile wärmer oder kühler, würden die Werte minimal verfälscht, weil Metall sich bei Wärme ja ausdehnt und bei Kälte zusammenzieht.
Aber ein Abweichen von der Norm, und mag sie auch noch so hauchdünn ausfallen, kommt bei Rudolf und Holger Geiling nicht in Frage. Denn Präzision ist ein Merkmal für Qualität. Seit mittlerweile 30 Jahren.