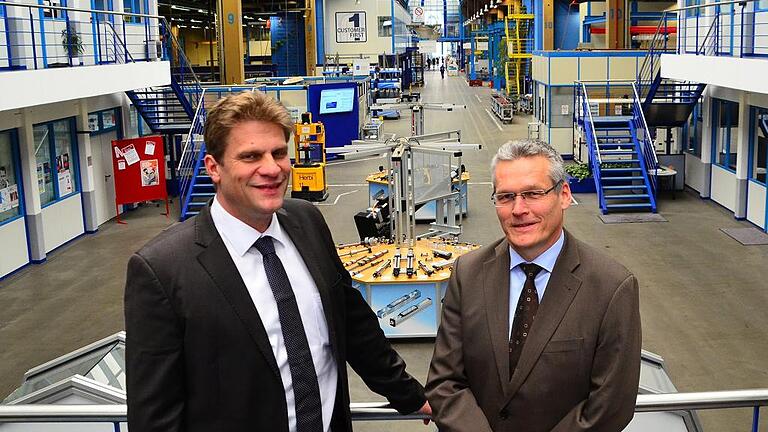
Die zufällige Begegnung am Ende des kleinen Rundgangs durch die die Fertigung ist ein schöner Beleg dafür, dass bei Bosch Rexroth im Schweinfurter Süden die Welt wieder in Ordnung ist. Als sich Harald Krug (54) und Matthias Rommel (47) zum Foto im zentrale Eingangsbereiches des Schweinfurter Werkes stellen, begegnet ihnen Winfried Werner, der Betriebsratsvorsitzende. Die Begrüßung ist freundlich locker, es wird ein bisschen gescherzt. Man versteht sich.
„Wir sind zurück in der Erfolgsspur“, sagt dann auch Krug, der für das Kaufmännische in der Lineartechnik von Bosch Rexroth verantwortlich ist. Während der Konzern im vergangenen Jahr beim Umsatz einen Rückgang von 2,5 Prozent bilanzieren musste, legte die Lineartechnik um sieben Prozent zu. Da die Branche nur um zwei Prozent wuchs, hat das Unternehmen also bei den Marktanteilen zugelegt. „Wir haben Kunden zurückgewonnen“, freut sich Krug und sieht die Arbeit der letzten zwei Jahre bestätigt.
„2016 war unser Rekordjahr“, sagt Krug und blickt bis 2014 zurück, als das Unternehmen einen Restrukturierungsprozess einleiten musste, den er schmerzhaft nennt. Aus Kostengründen mussten Teile der Produktion nach Blaj in Rumänien verlagert werden. Das hat in den Werken Schweinfurt und Volkach 300 Arbeitsplätze gekostet. Einige Mitarbeiter konnten zu Bosch nach Bamberg versetzt werde. Für alle habe man gemeinsam mit dem Betriebsrat sozialverträgliche Lösungen gefunden, erklärt Krug, der 2013 nach Schweinfurt kam.
Mehr Verantwortung vor Ort
Mit der Umstrukturierung, bei der der Konzern mehr Verantwortung an die einzelnen Werke gegeben hat, verbunden war die klare Erklärung, dass Schweinfurt das Leitwerk für die Lineartechnik von Bosch-Rexroth bleiben wird. Die Einheit stellt Produkte her, die zur präzisen, sicheren und energieeffizienten Bewegung von Maschinen und Anlagen sorgen. In Schweinfurt sind dies Achsen und Linearführungen, die in Maschinen und Anlagen von Fabriken, aber beispielsweise auch in Schleusen oder in der Bühnentechnik eingesetzt werden.
Damit ist Bosch Rexroth mit 2800 Mitarbeitern in Europa die Nummer eins und liegt weltweit auf Rang zwei. Um diese Position zu sichern, wurden gemeinsam mit den Beschäftigen sämtliche Prozesse auf den Prüfstand gestellt und neu geordnet, sagt Krug. Dass dies erfolgreich war, beweist nicht nur die Bilanz für 2016, sondern auch das erste Quartal 2017. „Wir sind weiter auf Rekordniveau und verdienen wieder richtig Geld.“ Dazu beigetragen hat auch, dass es gelungen ist, die Lieferzeiten deutlich zu verringern – von zehn auf ein bis zwei Tage.
Inzwischen wird das Personal wieder aufgestockt. In Schweinfurt sind es aktuell knapp 1400 und in Volkach 340 Mitarbeiter. Mit der Eröffnung einer eigenen Ausbildungswerkstatt im Herbst letzten Jahres, zuvor wurde gemeinsam mit dem ehemaligen Schwesterunternehmen ZF ausgebildet, wurde zudem ein Zeichen für die gewachsenen Ansprüche gesetzt.
Alle Bereiche positiv
„Ich bin beeindruckt, was hier geleistet wurde“,sagt Matthias Rommel, der technische Leiter für die Lineartechnik, der im August nach Schweinfurt gekommen ist. Alle Produktgruppen entwickelten sich positiv.
Auf der Hannover Messe vor wenigen Wochen, die ganz dem Thema Industrie 4.0 gewidmet war, hat Bosch Rexroth präsentiert, dass das Unternehmen ambitioniert unterwegs ist. Es geht darum, Mechanik und Elektronik immer besser miteinander zu kombinieren. Sensoren sollen es der Maschinen ermöglichen, sich selbst zu überwachen und selbst zu steuern. „Dafür werden Komponenten benötigt, die intelligenter als die heutigen sind“, sagt Rommel. Dafür bedürfe es vieler kleine Schritte.
Industrie 4.0
Werkleiter Clemens Maginot führt in den Bereich, in dem Führungsschienen geschliffen werden. Dort lässt sich das Prinzip von Industrie 4.0 gut erklären. Nach und nach werden die Maschinen ersetzt beziehungsweise nachgerüstet. An zwei nagelneuen Maschinen wurde dank modernster Sensortechnik und Vernetzung des gesamten Prozesses die Präzision bereits um den Faktor sechs erhöht, berichtet André Etzel, der hier Verantwortung trägt. Da bewegt man sich im Bereich von „My“, tausendstel Millimetern, der höchsten Qualitätsstufe. Ein Mitarbeiter hat zwar ein Auge auf den Messwerten, das Nachstellen der Maschine geschieht jedoch elektronisch.
Damit steigt die Qualität, die Fehlequote sinkt. Das überzeugt die Kunden. Wenn Krug und Rommel nach vorne schauen, dann tun sie dies mit großem Optimismus. Das spürt man.