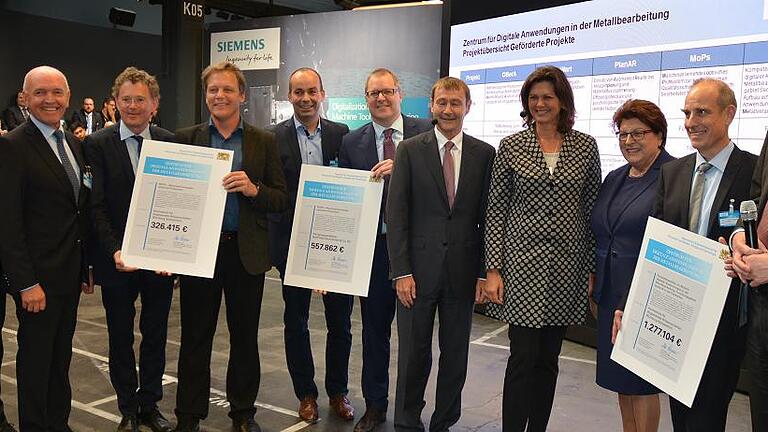
Rund um die neue Arena der Digitalisierung hat die Siemens AG erstmals einen Kongress veranstaltet. Thema der zweitägigen Veranstaltung war die Digitalisierung in der Metallbearbeitung. Zum Abschluss lobte Wirtschaftsministerin Ilse Aigner den Kongress und überbrachte Förderbescheide für zwei neue Projekte. Die beiden geförderten Maßnahmen für neue digitale Anwendungen im Bereich der Metallbearbeitung haben ein Gesamtvolumen von 3,1 Millionen Euro. Und sie sind erst der Auftakt einer mit 10 Millionen Euro geförderten Zentrumsgründung für digitale Anwendungen, die rund um Siemens in der Kreisstadt entstehen soll.
100 Teilnehmer beim Kongress
Rund 100 Teilnehmer verzeichnete Siemens beim ersten Kongress zum Thema „Digitalisierung in der Metallbearbeitung – Chancen für Industrie, Mittelstand und Wissenschaft“. In der neuen Arena der Digitalisierung in den Siemens-Hallen sowie in der Stadthalle informierten sich die Teilnehmer über neue Möglichkeiten rund um das Thema Digitalisierung, die sowohl kleinere und mittelständische Unternehmen wie auch große Industriebetriebe vor neue Herausforderungen stellt. Unternehmen der Fertigungstechnik müssen auf immer differenziertere Kundenwünsche eingehen bei gleichzeitig zunehmenden Anforderungen an Individualisierung und Qualität.
Beim Digitalisierungskongress wurden nun Chancen und Potenziale sowie die Auswirkungen auf den industriellen Wandel von Fachleuten aus Hochschule wie auch Vertretern von Werkzeugmaschinenbauern sowie Experten von Siemens diskutiert.
„Die Digitalisierung hält längst Einzug in die verarbeitende Industrie“, sagte Siemens-Vorstand Klaus Helmrich bei der Abschlussveranstaltung in der Arena der Digitalisierung. Insbesondere hob Helmrich das Zusammenspiel von Anwendern, Herstellern und Wissenschaft hervor und bekräftigte, den Kongress sukzessive zu einer Jahrestagung für digitale Anwendungen des Mittelstands in Bad Neustadt ausbauen zu wollen. „Diese richtet sich an Partner in der Region ist aber auch offen für andere Unternehmen“, so Helmrich.
Zur Abschlussveranstaltung waren eigens Landtagspräsidentin Barbara Stamm, der Landtagsabgeordnete Sandro Kirchner sowie die Staatsministerin für Wirtschaft und Medien, Energie und Technologie, Ilse Aigner gekommen. „Die Digitalisierung ist der zentrale Innovationstreiber in der Wirtschaft, gerade auch in der Metallverarbeitung“, sagte Aigner. „Wir wollen die hier in der Region vorhandenen Kompetenzen weiter stärken und die Unternehmen vor Ort fit machen für die digitale Zukunft.“
Bad Neustadt soll in diesem Zusammenhang laut Aigner zu einem „Zentrum für digitale Anwendungen in der Metallverarbeitung“ werden. „Die ersten beiden Projekte sind jetzt startklar und werden vom Bayerischen Wirtschaftsministerium mit rund 2,2 Millionen Euro gefördert“, sagte die Ministerin bei der Förderbescheidübergabe. Aigner weiter: „Ich bin zuversichtlich, dass wir zusammen mit Wirtschaft und Wissenschaft wichtige Impulse für eine nachhaltige Entwicklung in der Region setzen können. Dafür stehen uns in den kommenden Jahren insgesamt zehn Millionen Euro zur Verfügung.“ Zudem verwies Aigner darauf, dass der Aktionsplan für Bad Neustadt erste Erfolge zeigt: „Nach den von Siemens bekannt gegebenen Umstrukturierungsmaßnahmen haben wir umgehend mit einem Aktionsplan reagiert. Durch Förderung innovativer Themenfelder wie Industrie 4.0 und Telemedizin erschließen wir Zukunftspotenziale für die Region. Vor allem im Bereich Elektromotoren beziehungsweise Automotive ist hier viel Know-how vorhanden, an das wir nahtlos anknüpfen können.“
Anschubfinanzierung für Projekte
Die ersten beiden vom Wirtschaftsministerium geförderten Projekte erhalten nun ihre Anschubfinanzierung. Partner bei allen Projekten sind die Siemens AG und Hochschule Würzburg-Schweinfurt. Das Forschungsgebiet Sensorik in der Produktion (ProDiMe) wird vollständig an der Hochschule Würzburg-Schweinfurt unter zukünftiger Einbeziehung bayerischer Unternehmen umgesetzt und erhält eine Förderung in Höhe von 1,3 Millionen Euro (Gesamtvolumen 1,7 Millionen Euro).
Ein maschinell lernendes optisches Prüfsystem (MoPs) wird von der Firma Fertigungsgerätebau A. Steinbach GmbH & Co. KG aus Salz in Zusammenarbeit mit Siemens und der Hochschule Würzburg-Schweinfurt entwickelt. Fördergelder des Wirtschaftsministeriums gehen hier an die Hochschule (326 415 Euro) sowie an die Firma FGB Steinbach (557 862 Euro). Das Gesamtvolumen dieses Projektes beläuft sich auf 1,6 Millionen Euro.
Die geförderten Projekte
Schwerpunktpartner bei beiden Projekten sind die Siemens AG und Hochschule Würzburg-Schweinfurt. Weitere Partner werden je nach Konzept beteiligt. Zwei Projekte wurden nun bewilligt:
Projekt 1: ProDiMe
Kompetenzaufbau im Bereich digitaler Anwendungen in der Metallbearbeitung; Forschungsgebiet Sensorik in der Produktion (ProDiMe): Ziele des Projektes sind die Erweiterung einer Experimentierplattform für die Betrachtung additiver Metallverarbeitung, die Integration neuer Messverfahren (neben optischen Methoden etwa auch Oberflächenwellen, Piezoverfahren, etc.) für Temperatur bzw. thermophysikalischer Größen in die Prozesstechnik- und Fertigungstechnik in die Experimentierplattform und der Aufbau eines regionalen Netzwerks im Bereich Sensorik für die industrielle Metallverarbeitung. Im Vordergrund steht dabei der Technologietransfer durch die Einbindung weiterer Industriepartner und mittelfristig die Verstetigung der Projektgruppe.
Das Projekt wird vollständig an der Hochschule Würzburg-Schweinfurt unter zukünftiger Einbeziehung bayerischer Unternehmen umgesetzt und ist auf vier Jahre angelegt.
MoPs:
Maschinell lernendes optisches Prüfsystem (MoPs): Ziel des Projekts ist die Entwicklung eines neuartigen, optischen Prüfverfahrens für die Qualitätssicherung im Nachgang von metallverarbeitenden Prozessen. Das Verfahren besteht zum einen aus einem Kamerasystem und einer Auswertemethode, die Algorithmen aus dem Bereich des maschinellen Lernens (Künstliche Intelligenz) zur Analyse der Bildaufnahmen implementieren soll. Neben der optischen Prüfmethode kommt auch das Wirbelstromprüfverfahren zur Risserkennung zum Einsatz. Beide Systeme werden zusammen in eine Prüfmaschine integriert und können in Kombination zukünftig viel zuverlässiger Bauteilfehler finden. Die selbstlernende Anlage soll eine Beurteilung der geprüften Bauteiloberfläche mit hohen Erkennungsraten ermöglichen und damit eine Kategorisierung des Qualitätszustands in „gut“ oder „schlecht“ unter Serienproduktionsbedingungen erlauben. Die Grundlage für die Kategorisierung stellt die Detektion von Verfärbungen und Fehlstellen, wie Rost, Schleifbrand, Kratzer oder Risse auf der Oberfläche der Prüflinge dar.
Derartige Schäden führen bei Präzisionsmetallbauteilen häufig zum Ausfall der kompletten Baugruppe, falls sie nicht im Rahmen der Qualitätssicherung entdeckt werden. Projektbeteiligte sind die Hochschule Würzburg-Schweinfurt und die Firma FGB Steinbach aus Salz. krit