
Der Parkplatz vor GKN Sinter Metals & Forge Operations in Bad Brückenau, kurz vor 14 Uhr - Personalwechsel. Die Mitarbeiterinnen und Mitarbeiter der Frühschicht gehen, die der Spätschicht kommt. Alles wie immer. Doch das Werk und seine Angestellten haben in den vergangenen drei, vier Jahren einen Wandel erlebt, der von der Flutkatastrophe im Ahrtal 2021 mit angestoßen wurde.
Mehr als 15 Millionen Euro investiert
Eigentlich könnte sich Thomas Schaab, seit 17 Jahren in der Firma und seit 2021 Werkleiter, entspannt zurücklehnen. Mehr als 15 Millionen Euro hat der Mutterkonzern GKN Powder Metallurgy in den Brückenauer Standort investiert; die Produktion läuft auf Volllast. „Zusammen mit den Technologien, die wir reinbekommen haben, ist das ein Vertrauensbeweis gegenüber den Mitarbeitern", sagt der gebürtige Riedenberger und studierte Maschinenbauingenieur. Ein Vertrauen, das man zurückzahle.
Die Investitionen und der Zuwachs an Technologie bedeuteten aber auch eines: viel Arbeit. Ganze Hallenbereiche wurden freigeräumt, um sie mit neuen Maschinen zu bestücken. Produktionsabläufe wurden eingeübt.
Sinterschmiedeprozess seit zweitem Quartal 2022
Die größte Neuerung ist dabei, dass in Bad Brückenau seit dem zweiten Quartal 2022 der Sinterschmiedeprozess beheimatet ist. Dieser meint das extreme Nach-Verdichten (Schmieden) bereits produzierter Vor-Formen.
Sinterbauteile entstehen, indem stark verdichtetes Metall-Pulver (sogenannte Presslinge) bei rund 1.100 Grad Hitze zu einem Bauteil „versintert“ werden. Ohne das Sintern ist das Metallpulver sehr instabil und kann teilweise mit Muskelkraft zerbrochen werden. Um die hohen Kräfte auszuhalten, wie sie beispielsweise auf Synchronisierungsbauteile im Autogetriebe herrschen, ist eine hohe Festigkeit notwendig. Um nach dem Sintern die Festigkeit noch weiter zu steigern, wurde das Sinterschmieden entwickelt.
Dies geschieht ebenfalls unter großer Hitze. Allerdings werden die Sinterteile diesmal über Induktion mit Strom auf mehr als 1000 Grad Celsius erhitzt und danach in der Schmiedepresse verdichtet. „Sie haben dann eine Dichte wie Vollstahl", sagt Werkleiter Schaab.
Sinterschmieden ursprünglich in Hückeswagen im Ahrtal
Dass das Schmieden nach Bad Brückenau gekommen ist, hat auch mit der Flutkatastrophe im Ahrtal vom Juli 2021 zu tun. Ursprünglich war der Prozess in Hückeswagen, einer Kleinstadt in Nordrhein-Westfalen, angesiedelt. Rund 40 Menschen waren laut Schaab dort beschäftigt.
Als die Flut durch war, konnte der zuvor gesunde Standort im Ahrtal nicht weiterproduzieren. „Der wirtschaftliche Schaden war irreparabel", so Schaab. Die Brückenauer Kollegen sprangen ein, übernahmen kurzfristig die Vorfertigung.
Konzernentscheidung half, Arbeitsplätze zu sichern
Zwar kam der Schmiedeprozess in Hückeswagen wieder notdürftig in Gang. Doch schließlich entschied die Konzernzentrale, „die Schmiedekompetenz neu aufzusetzen und auszubauen", so der Rhöner Werkleiter. „Die Entscheidung hat uns in Bad Brückenau geholfen, Arbeitsplätze zu sichern", ergänzt er.
Sowohl Sintern als auch Schmieden sind energieintensiv. 20 Gigawattstunden Energie benötigt das Bad Brückenauer Werk im Jahr; das entspricht dem Verbrauch von 4.000 bis 5.000 Privathaushalten. Deswegen spielt das Thema Energiesparen im GKN-Werk Bad Brückenau eine bedeutende Rolle - auch, um auf dem Weltmarkt konkurrenzfähig zu bleiben.
Bad Brückenauer Schmiedeprozess spart Energie
Der Schmiedeprozess in Bad Brückenau ist besonders effizient und energiesparend. Gegenüber dem ursprünglichen Prozess in Hückeswagen werden mehr als 3.000 Tonnen Kohlendioxid pro Jahr eingespart.

Im Januar ist eine 680-Kilowatt-Photovoltaikanlage auf den Bad Brückenauer GKN-Dächern in Betrieb gegangen. Kosten: eine Dreiviertelmillion Euro. Die PV-Anlage trägt 600.000 Kilowattstunden im Jahr zur Grundlast des Werkes bei, so Arnold Scheller aus dem Bereich Einkauf. Ihm zufolge bezieht das Unternehmen in der Rhön die Hälfte seines Gesamtstroms aus grünen Quellen, aus Photovoltaik, Wind- und Wasserkraftanlagen.
Weitere hohe Investitionen geplant
In Zukunft wird die Abwärme-Rückgewinnung aus den Sinteröfen noch mehr im Fokus stehen. Investitionen von einer Viertelmillion Euro sind geplant. „Wir werden in unserem Werk keine Autarkie erreichen; aber wir wollen die Energie möglichst nachhaltig nutzen", sagt Thomas Schaab.
Zum Erhalt des Bad Brückenauer Standortes tragen auch andere Faktoren bei. Technologie, Entwicklung und ein eigener Werkzeugbau helfen, Kundenanfragen schnell zu realisieren. Es entstehen kreative Ideen für Produkte aus Metallpulver. Auch die Beherrschung der komplexen Anlagen—und Steuerungstechnik durch gut ausgebildete Mitarbeiter ist ein enorm wichtiger Punkt. Mitentwickelt wird auch an der Speicherung von Wasserstoff (wir berichteten).
Produktion für letzte Generationen von Verbrennern
Zurzeit wird noch schwerpunktmäßig für die letzten, aber ausgereiften Generationen Verbrenner-Fahrzeuge produziert. Der Markt geht aber mehr in Richtung Elektroantrieb, beziehungsweise besser gesagt: zur Verschmelzung beider Technologien. „Auch hybridtechnisch sind wir voll auf der Höhe", sagt Thomas Schaab.
Der GKN-Konzern betreibt weltweit 27 Werke mit mehr als 5.000 Mitarbeitern. 350 davon arbeiten in Bad Brückenau. Jährlich werden weltweit für 100 Kunden 200 verschiedene Bauteile produziert - und zwar in Gesamtzahlen von 16 Millionen Stück. 75 Prozent der Teile werden für die Automobilbranche hergestellt, 20 Prozent davon für den Schwerlastbereich. Zehn Prozent der Produktion fließen in elektrische Anwendungen beziehungsweise Fahrzeuge, fünf Prozent in die Industrie.
Werk verarbeitet fast nur Metallschrott
Das Bad Brückenauer GKN-Werk verarbeitet in seinen 20 Pressen jährlich 7.500 Tonnen Metallpulver. 96 bis 97 Prozent davon stammen aus der Schrottverwertung, der Materialkreislauf ist somit nachhaltig und geschlossen. Dazu kommen Zuschlagsstoffe wie Graphit, Kupfer und umweltfreundliche Wachse als Schmiermittel für die Produktion.
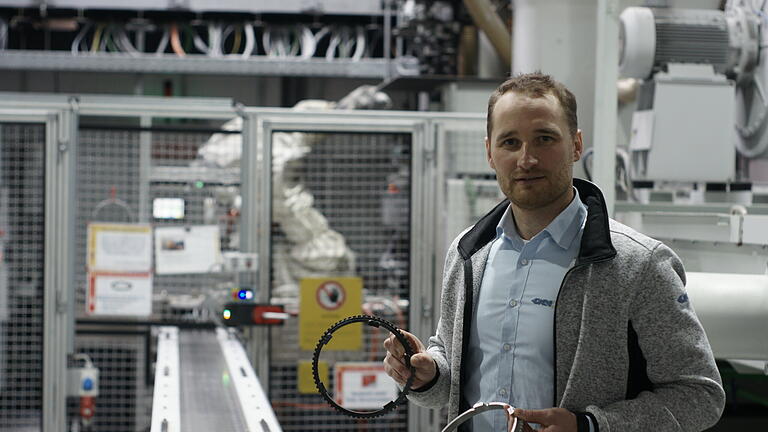