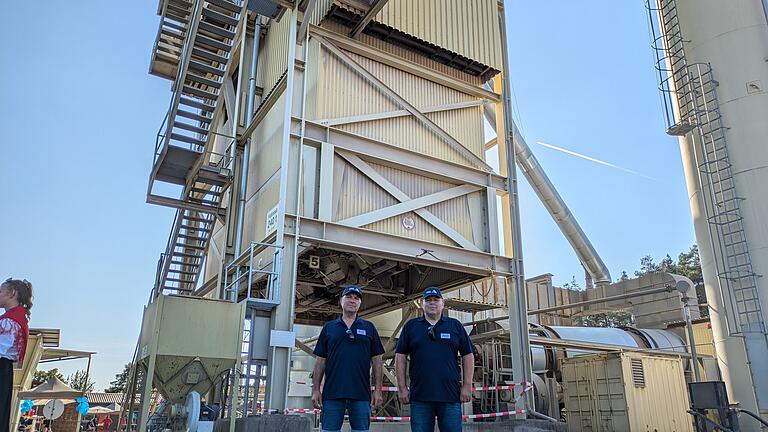
Es ist von verschiedenen Bergen aus zu sehen – und wenn der Wind in eine bestimmte Richtung weht, dann riecht man es auch: das Asphaltmischwerk am Münnerstädter Schindberg in den Kurven der B19. Die Brüder Michael und Heiko Erhard arbeiten in der Anlage, die ein Werk der Asphaltmischwerke Main-Saale (Schweinfurt) ist, seit 20 Jahren zu zweit.
"Wir verstehen uns super, verstehen uns oft auch ohne Worte", berichtet Michael Erhard. Ihr tägliches Geschäft ist das, auf dem wir täglich Auto fahren, laufen oder radeln: Asphalt. Rund 60.000 Tonnen mischen sie im Jahr. Beim Tag der offenen Tür konnten Interessierte sich die Produktion genauer ansehen und in den großen Turm blicken.
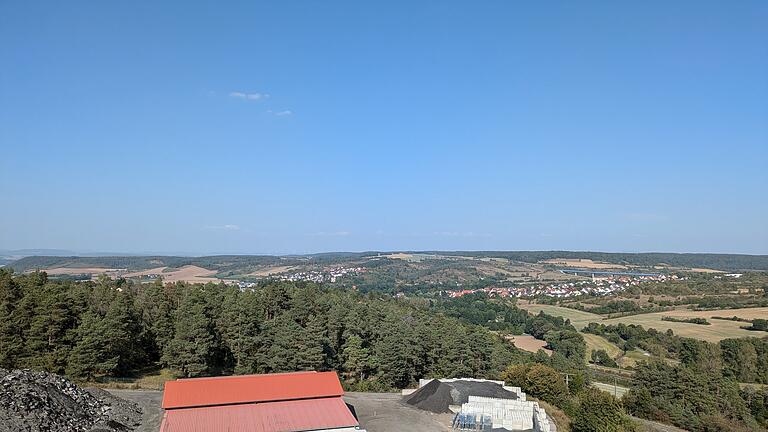
Kleine Steine sind ein Baustein
Ein Teil der Asphaltmischung sind kleine Steine – die gibt es in verschiedenen Größen und Arten. Diese sind auch ziemlich regional: "Der Basalt kommt aus Bischofsheim oder Maroldsweisach, der Kalk vom Kalkwerk Salz, Natursand aus Dettelbach", weiß Michael Erhard. Je nachdem, was gebraucht wird, ist einer der beiden damit beschäftigt, die verschiedenen Steinsorten mit einem Radlader in die sogenannten Dosseure zu kippen: nach unten geöffnete Behälter, die nach einer vorgegebenen Dossiermenge eine bestimmte Menge der Steinsorte auf das Förderband lassen.
Vom Förderband aus werden die kleinen Steine in eine sich drehende Trommel geschüttet. Darin befindet sich ein Brenner, der das Mischgut auf 250 bis maximal 400 Grad erhitzt - zum Trocknen, und damit es mit dem heißen Bitumen vermischt werden kann, ohne dieses abzukühlen. "Wir befeuern mit Braunkohle. Aber wir werden mit einer neuen Anlage bald öfter in der Lage sein, Niedrigtemperaturasphalt zu fahren. Dann brauchen wir nicht mehr so viel Energie und damit weniger Kohle", erklärt Erhard.
Straßen werden zu 100 Prozent recycelt
Ein anderer Teil in der Asphaltmischung ist Recyclingasphalt. Davon ist auf dem Gelände ein hoher Berg gelagert – er besteht aus ausgebaggerten Straßenteilen, teilweise noch in riesigen Stücken. Dieser wird gebrochen und alles davon kann wiederverwendet werden. Als Erhard vor 20 Jahren hier angefangen hatte, gab es das noch nicht. Pro Mischung können bis zu 50 Prozent zugemischt werden. "Derzeit wird eine Halle gebaut, in der wir den Recyclingasphalt trocken lagern können. Das spart ebenfalls Energie, die wir nicht mehr zum Trocknen brauchen", so Erhard. Energie sei in der Produktion am teuersten.
Bitumen und Steinmehl als weitere Zutat
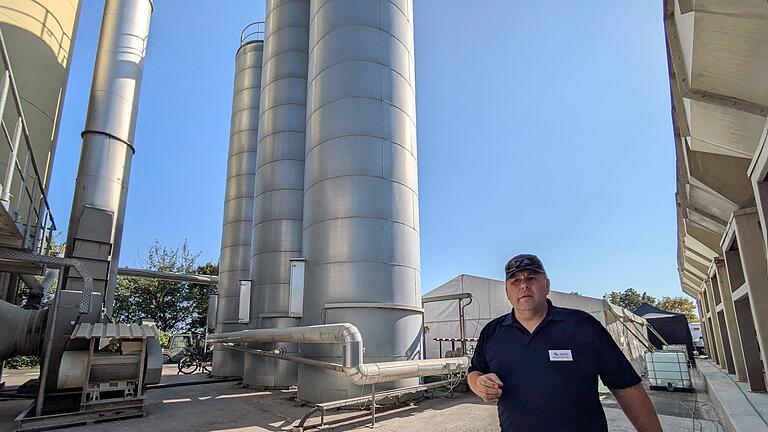
Die drei metallenen Tanks neben dem Turm sind Bitumentanks. Bitumen hat den seit 1984 im Straßenbau verbotenen Teer abgelöst und ist ein klebriges Kohlenwasserstoff-Gemisch. Ein Tank fasst etwa 50 bis 55 Tonnen – also rund zwei LKW-Ladungen. "Die sind das ganze Jahr auf 160 Grad beheizt, damit das Material schön geschmeidig bleibt und sich gut verarbeiten lässt", erklärt Erhard.
Die gelben dünneren Silos beinhalten Steinmehl, das zum einen aus der eigenen Produktion stammt (Eigenfüller), zum anderen von Firmen zugekauft wird (Fremdfüller). Es fungiert als Bindemittel.
Damit steht das Grundrezept für Asphalt: verschiedene Steine, darunter zerkleinerter Recyclingasphalt, Bitumen und Steinmehl. Je nach Wunsch kommen diverse Zugaben dazu. Beim Asphalt, den die Anlage derzeit für die Baywa-Kreuzung in Bad Neustadt mischt, sind beispielsweise kleine Aramidfasern beigegeben, die dafür sorgen sollen, dass der Asphalt sich beim Bremsen nicht zusammenschiebt oder Spurrillen bildet. Bei Autobahn-Asphalt wird Zellulose zugemischt, der ebenfalls festigen soll.
Vermischung und Lagerung im Turm
Nun geht es ein paar Stockwerke nach oben. Ganz oben kommt das heiße Steingemisch an, das meist gesiebt wird, bevor es ein Stockwerk nach unten in einen Bunker fällt. Dort können bis zu 160 Tonnen Steine über Nacht heiß gelagert werden. An der Unterseite der Bunker ist ein Raum, der aus verschiedenen Waagen besteht: eine für Bitumen, eine für Steinmehl, eine für die Steinmischung und eine für das Recyclinggemisch.
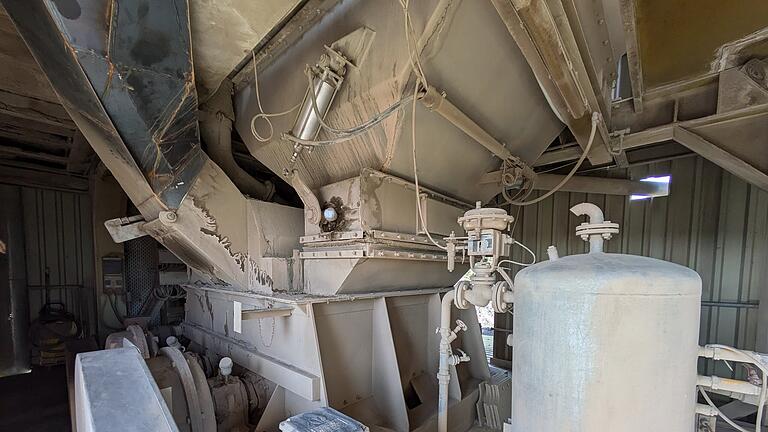
Wiederum ein Stockwerk weiter unten befindet sich das Herzstück der Anlage: der Mischer. Darin befinden sich zwei Mischwellen, die durch Elektromotoren angetrieben werden und die Masse gut vermischen. In der nächstniedrigeren Etage, der "Siloetage", fließt der fertige Asphalt in einen der fünf Silos hinein. Jedes der Silos kann 60 Tonnen bunkern – und wenn es voll ist, sogar über Nacht.
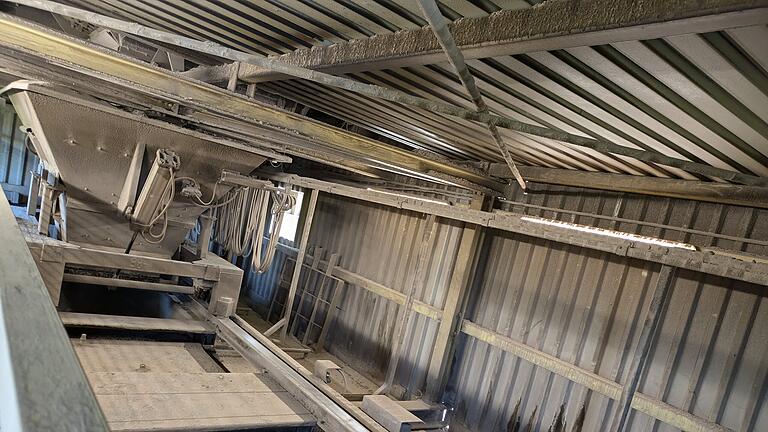
Wenn nun Kunden kommen, fahren diese einfach unter den Turm und das jeweilige Silo und lassen die flüssige Masse herunterlaufen. Ein Lkw kann etwa 26 Tonnen laden. Für eine Bundesstraße reicht das jedoch nur ein paar Meter.
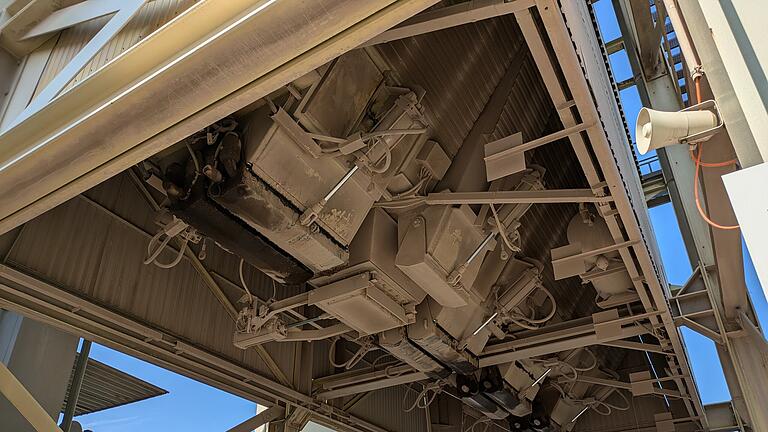
Eine Tonne Feinschicht kostet dabei rund 150 Euro die Tonne. Viele der Kunden sind Kleinkunden, etwa kleine Baufirmen. Größere Aufträge gab es beispielsweise beim Bau der Autobahn. Da lief das Werk auf Hochtouren.
Geschichte der Anlage
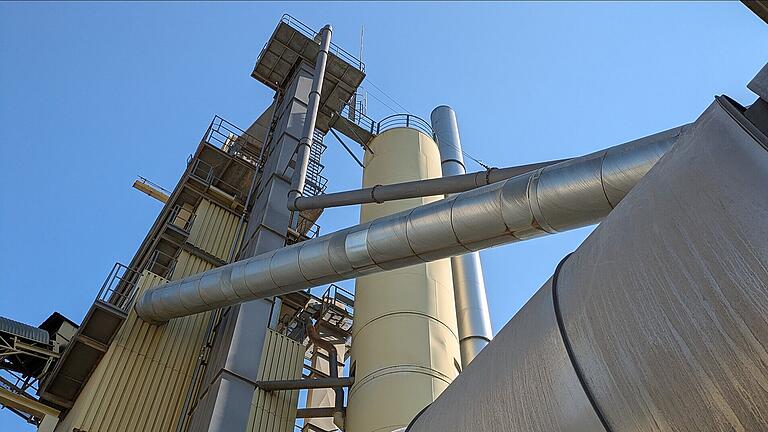
Früher war die Anlage im Besitz der Baufirma August Ullrich, erklärt Karlheinz Wolf, Geschäftsführer bei den Asphaltmischwerken Main-Saale. Daneben gab es die Baufirmen Stolz in Hammelburg, Glöckler in Grafenrheinfeld, Moll in Gänheim, Grümbel in Gössenheim. Um Fahrtwege zu reduzieren, schlossen sich die Firmen zusammen und gründeten 2000 die Asphaltmischwerke Main-Saale.